Honda CN250 2008 → Пластик. Ремонт, восстановление и танцы с бубном.
Пробило меня сегодня на посты. Что поделать, информации собралось много, она упорядочена и готова к постам. Можно и «пошкрябать пером», всё равно сезон у нас в городе кончился.
Итак, в данном посте речь пойдёт про ремонт и восстановление пластика. Не нужно мне говорить про «китайский пластик» и прочее-прочее-прочее. Проблема с пластиком есть как у «китайчи», так и у любой «Голды», разве что «драный китаец» выглядит не так страшно как «драная Голда». Да и я зря что ли купил себе газовое паяло? Кому интересно — под кат.

Ремонт пластика назрел с самого начала, но мне всё было как-то не до этого, а 19 сентября, закатываясь вечром в гараж я коцнул боковинку, что повлекло за собой полное оголение скутера и распайку пластика. Итак, «Лерой Мерленовская» сварочная проволока для АБС-а, газовый паяльник и дремель с фрезами — вот и всё, что нам понадобиться для восстановления пластика.
Фронт работ по мордашке на фото:

Передняя решётка, крепления и пластик боковин над «поворотниками-габаритами».
Фронт работ по корме на фото:

Тут у меня только верхний кофр и боковинка по левому борту. Фраза «только кофр» надо воспринимать как «собрать кофр из запчастей», поскольку основная масса работ пришлась как раз на него.
Пока восстанавливал мордашку было немного не до фотографий. Сначала забыл, а потом мне попал в глаз дым от «моментального клея», там я только успел паяльник выключить и выскочить на улицу. Как-то вообще не до фоток, когда у тебя глаз чуть ли не вытекает. Адовая вещь этот ваш цианакрилат, особенно если его зацепить горячим предметом. Руки бы с головой оторвал этому мастеру за такое вот. Тем не менее, придя в себя и вспомнив про то, что неплохо было бы отфоткать, немного извратился и снял уже установленную мордашку изнутра и снаружи. Да, качество отвратное, признаю, можно тапком в меня кинуть. Ещё одна тонкость — решётка тонкая, а потому её паять надо тоже тонкими прутками, я просто обтачивал наличествующие до нужной толщины. Если перегреете слишком сильно — геометрия «поплывёт» и вы намучаетесь выправлять, если вообще сумеете.


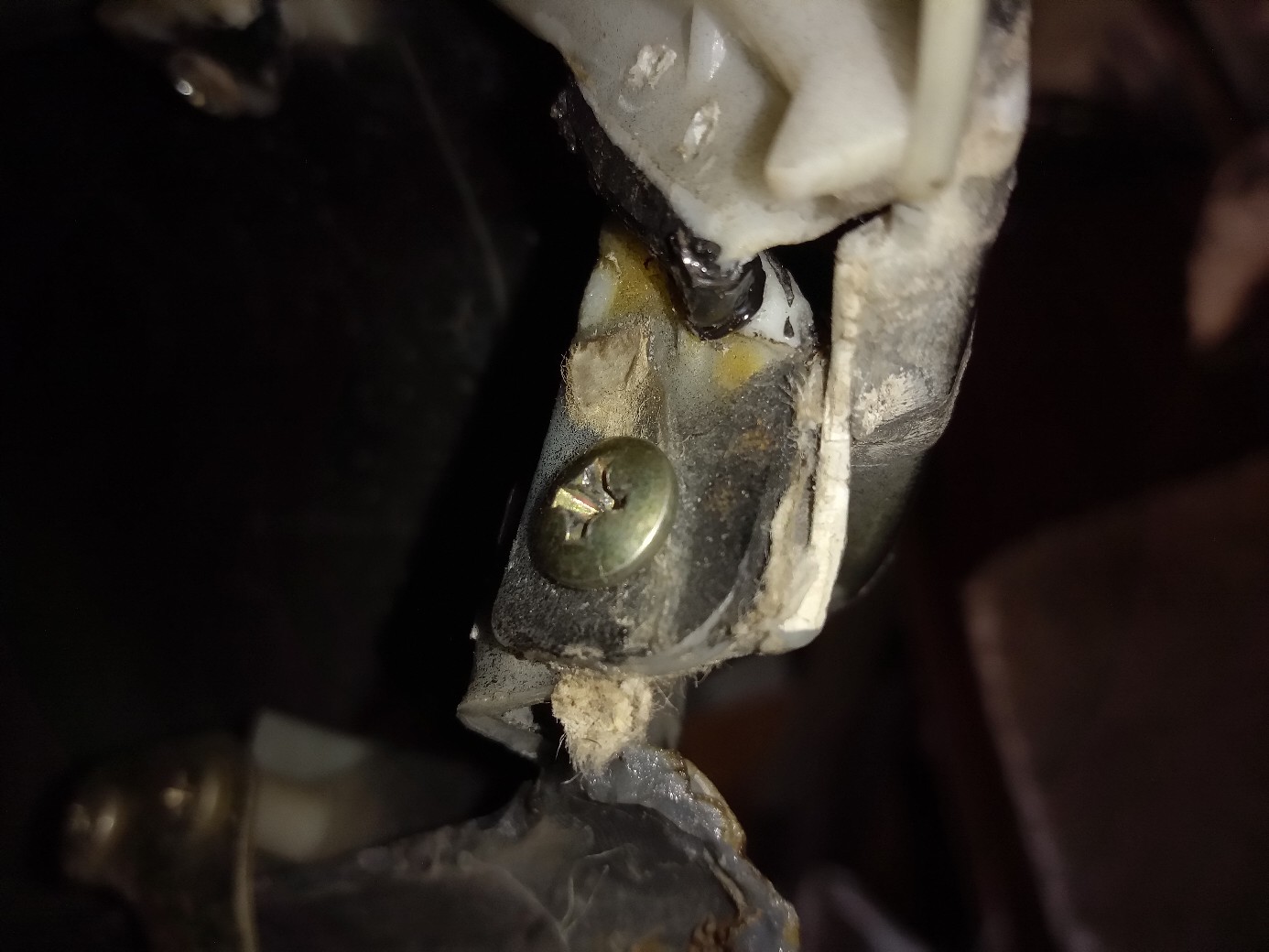

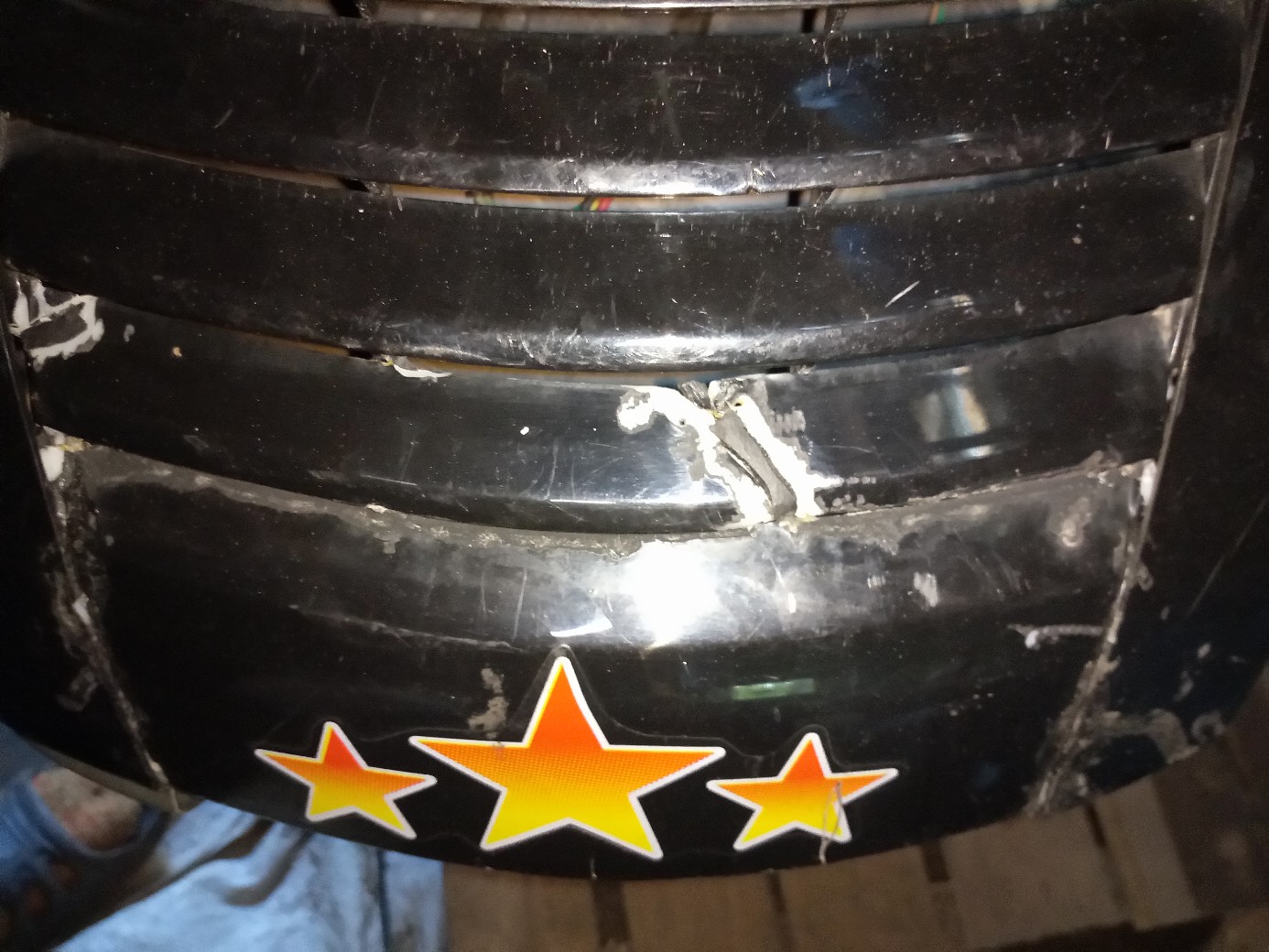

А вот с кормовой частью уже работал частично и с фотографиями процесса, когда вспоминал про них.
Сначала совмещаем детали и проходимся фрезой по стыку. Потом паяем одну сторону и повторяем с другой стороны. Если трещина сквозная или деталь вообще отпала — нужно наложить перемычки, дабы не лопнуло. После пайки подбираем всё лишнее фрезой — и готово. Собственно, вот и вся технология. Правда для её освоения придётся потрать не один вечер.
Фото детали изнутри, которую я обломил. Уже пропаяно.

Пропаиваем любые подозрительные места. Здесь я накосячил и перегрел пластик. Из-за чего поимел геморрой с выведением в более-менее нормальное состояние.


Главная проблема, которая у меня была по задним боковинам — это отсутствие креплений к раме, по одному переднему креплению с каждой стороны, из-за чего пластик громыхал как не в себя.
Наращиваем площадку.

И крафтим крепление. Самый лучший вариант — это надыбать кусок АБС-пластика (или полипропилена, или любого иного, из которого у вас исходная деталь) и вырезать из него подходящую деталь. У меня такого не было, потому пришлось проявить фантазию и паять из прутков. Долго, муторно, не очень красиво, но зато пластик по итогу держится очень добротно. Толщина — полтора-два прутка, поскольку я не очень угадал с расстоянием до рамы. А так — и прочности прибавило, и обрабатывать проще.



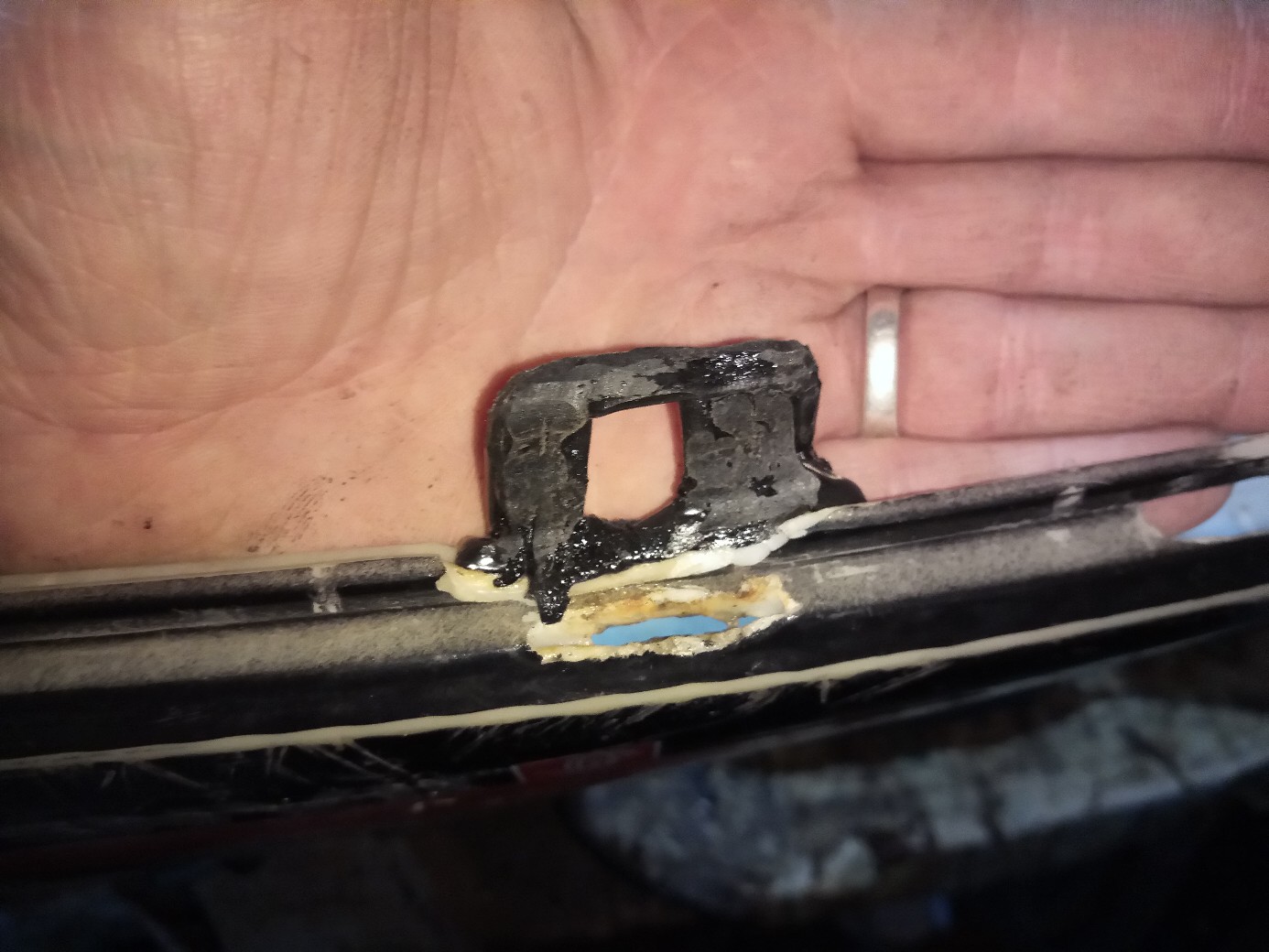

Теперь самое вкусное — кофр. Расстояния большие, всё держится одним куском — ляпота. Пропиливаем канавку и кладём шов. Повторяем пока не закроем все трещины. После чего убираем лишнее и радуемся результату.

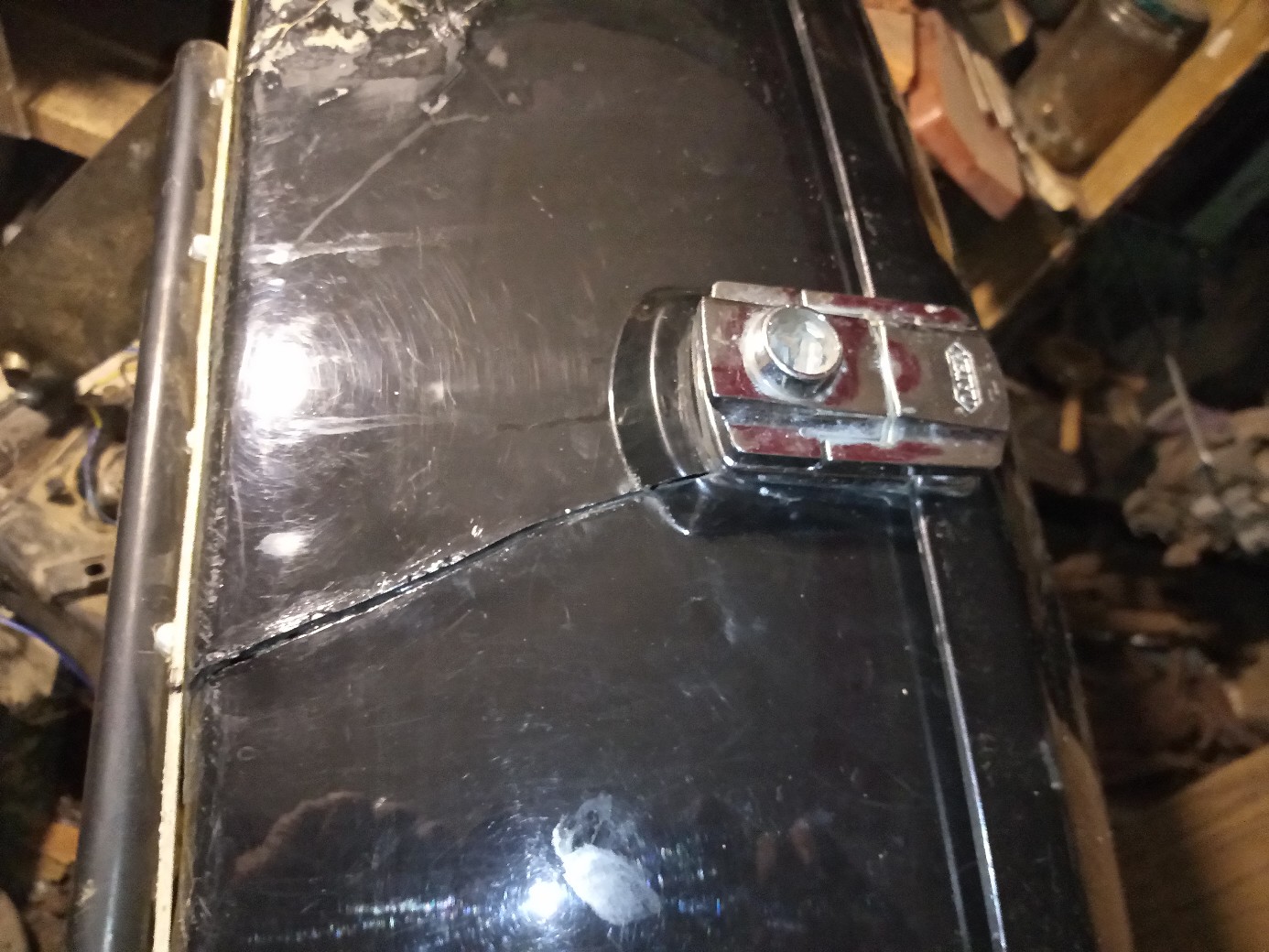



Ещё одна большая проблема — это отсутствие куска пластика на крышке кофра. Накидываем прутками нужную форму, обтачиваем — и вуа-ля, кофр становится почти как новенький.

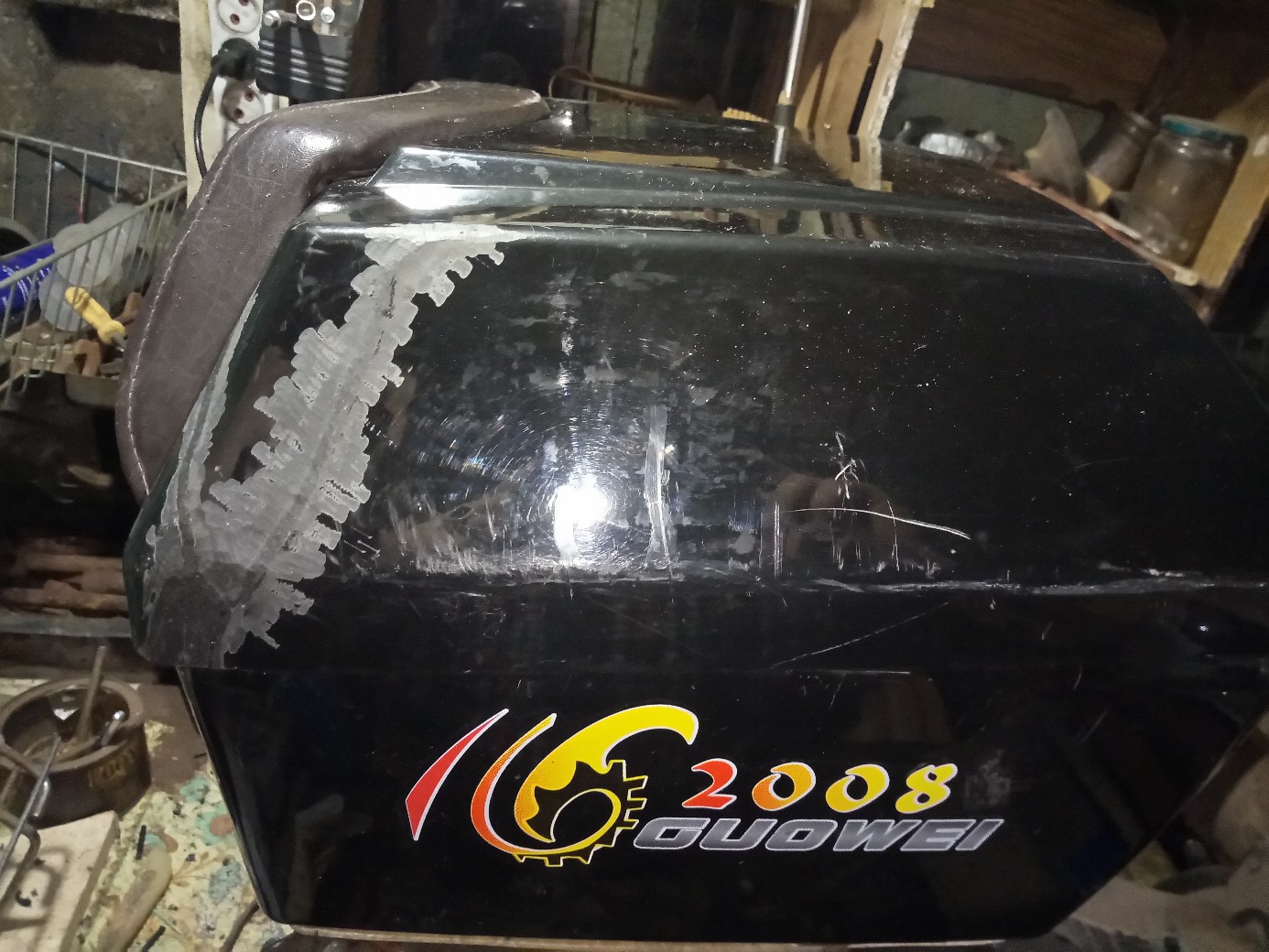
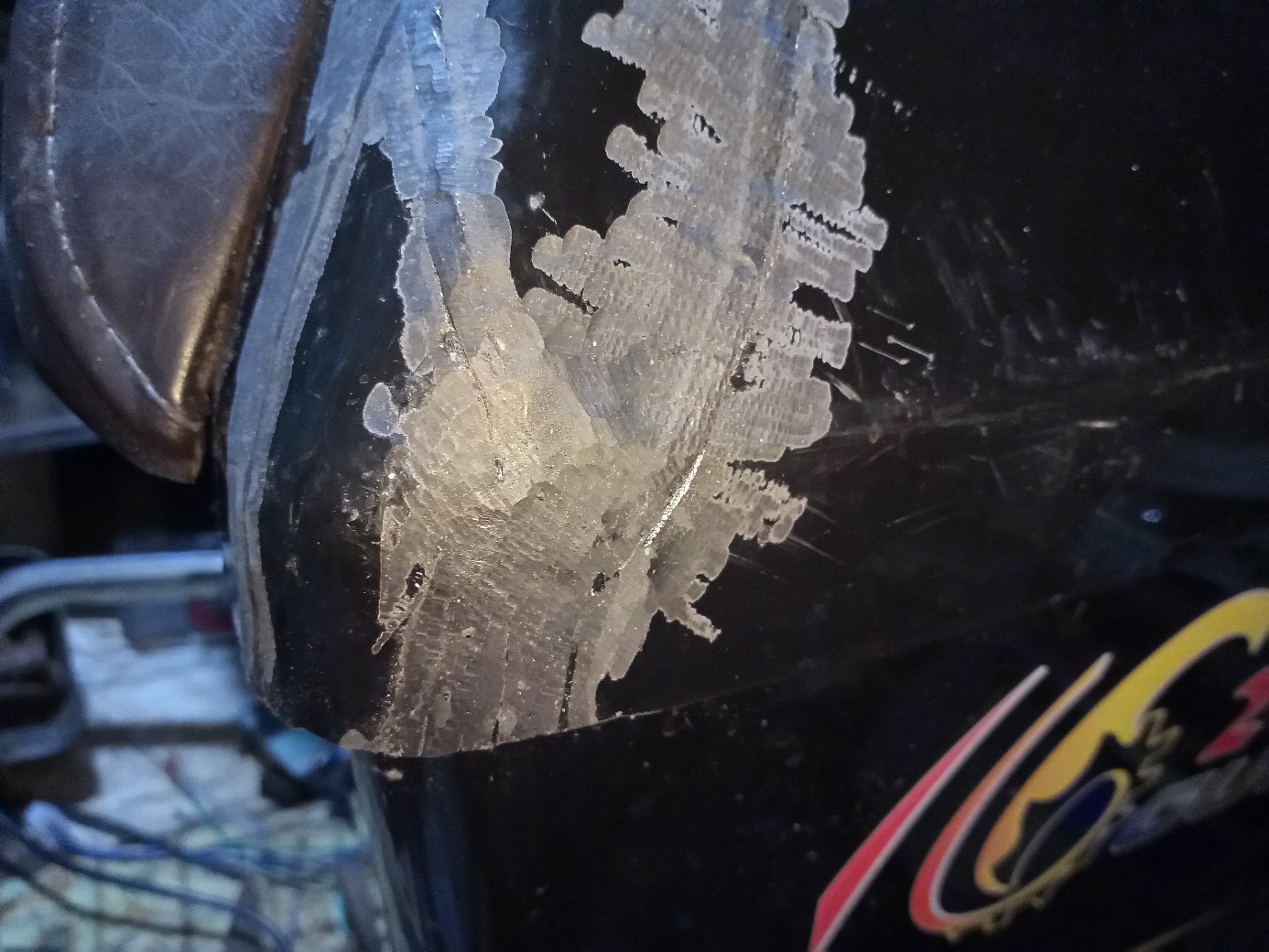

Единственное, что меня достаточно сильно напрягло — это то, что кофр был проварен только по наружной стороне. Внутри всё было пропаяно сеткой и залито эпоксидкой. Решение рабочее, но очень сильно уступает по надёжности проварке пластиком. Губить фрезы о стальную проволоку я не стал, так и оставил. Кофр никакой несущей нагрузки на себе не несёт, потому тут ничего страшного нет, но если бы были элементы несущими — пришлось бы как-то проходить трещины, дабы выкорчевать сетку.
На этом ремонт пластика у моего «Фужика» закончен. Теперь остаётся только покрыть шпаклёвкой по пластику, зачистить и прокрасить, избавившись от некошерных наклеек. Впрочем, лакокрасочные работы будут уже на следующий год. Всем удачи на дорогах.
Итак, в данном посте речь пойдёт про ремонт и восстановление пластика. Не нужно мне говорить про «китайский пластик» и прочее-прочее-прочее. Проблема с пластиком есть как у «китайчи», так и у любой «Голды», разве что «драный китаец» выглядит не так страшно как «драная Голда». Да и я зря что ли купил себе газовое паяло? Кому интересно — под кат.

Ремонт пластика назрел с самого начала, но мне всё было как-то не до этого, а 19 сентября, закатываясь вечром в гараж я коцнул боковинку, что повлекло за собой полное оголение скутера и распайку пластика. Итак, «Лерой Мерленовская» сварочная проволока для АБС-а, газовый паяльник и дремель с фрезами — вот и всё, что нам понадобиться для восстановления пластика.
Фронт работ по мордашке на фото:

Передняя решётка, крепления и пластик боковин над «поворотниками-габаритами».
Фронт работ по корме на фото:

Тут у меня только верхний кофр и боковинка по левому борту. Фраза «только кофр» надо воспринимать как «собрать кофр из запчастей», поскольку основная масса работ пришлась как раз на него.
Пока восстанавливал мордашку было немного не до фотографий. Сначала забыл, а потом мне попал в глаз дым от «моментального клея», там я только успел паяльник выключить и выскочить на улицу. Как-то вообще не до фоток, когда у тебя глаз чуть ли не вытекает. Адовая вещь этот ваш цианакрилат, особенно если его зацепить горячим предметом. Руки бы с головой оторвал этому мастеру за такое вот. Тем не менее, придя в себя и вспомнив про то, что неплохо было бы отфоткать, немного извратился и снял уже установленную мордашку изнутра и снаружи. Да, качество отвратное, признаю, можно тапком в меня кинуть. Ещё одна тонкость — решётка тонкая, а потому её паять надо тоже тонкими прутками, я просто обтачивал наличествующие до нужной толщины. Если перегреете слишком сильно — геометрия «поплывёт» и вы намучаетесь выправлять, если вообще сумеете.


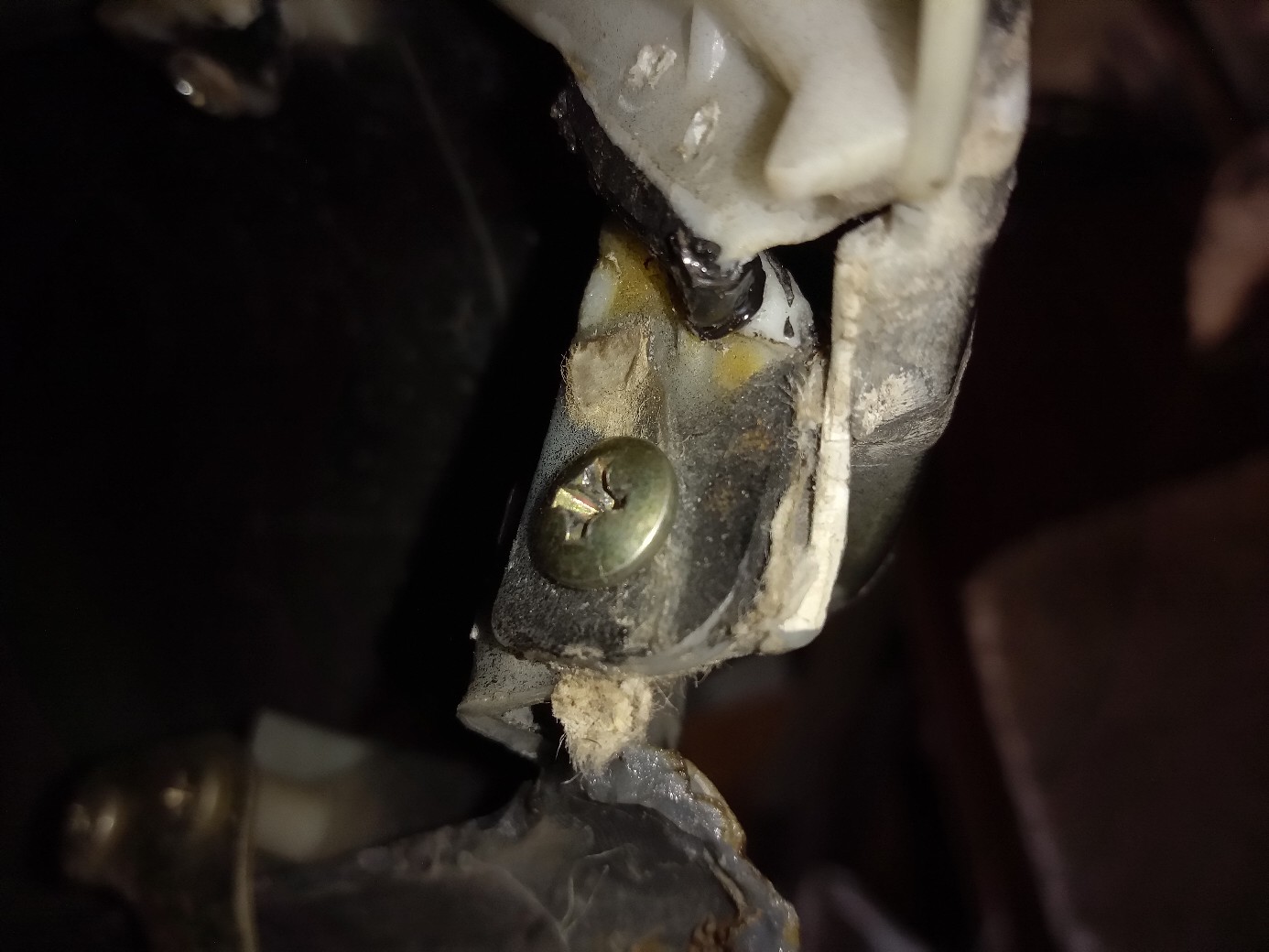

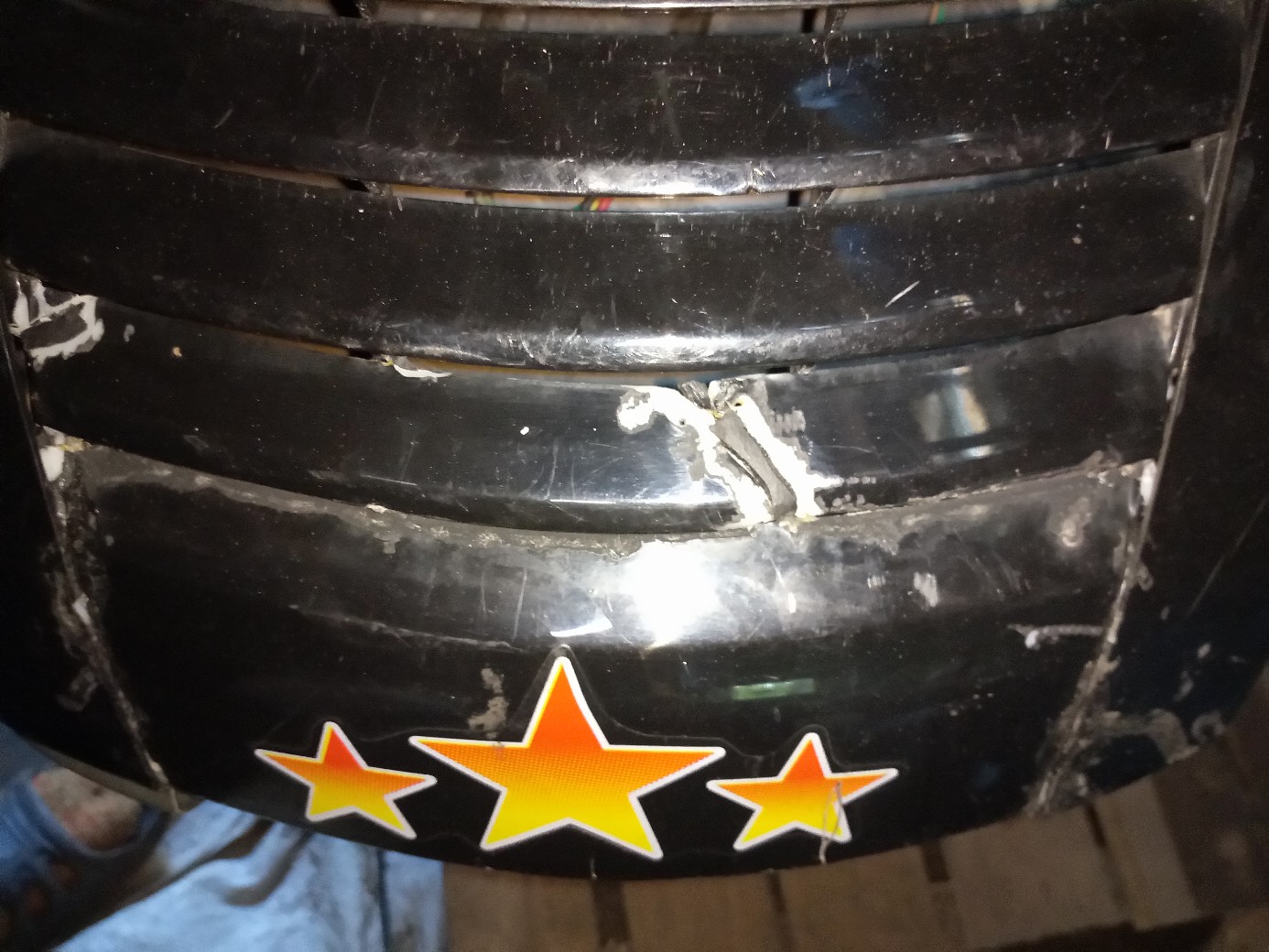

А вот с кормовой частью уже работал частично и с фотографиями процесса, когда вспоминал про них.
Сначала совмещаем детали и проходимся фрезой по стыку. Потом паяем одну сторону и повторяем с другой стороны. Если трещина сквозная или деталь вообще отпала — нужно наложить перемычки, дабы не лопнуло. После пайки подбираем всё лишнее фрезой — и готово. Собственно, вот и вся технология. Правда для её освоения придётся потрать не один вечер.
Фото детали изнутри, которую я обломил. Уже пропаяно.

Пропаиваем любые подозрительные места. Здесь я накосячил и перегрел пластик. Из-за чего поимел геморрой с выведением в более-менее нормальное состояние.


Главная проблема, которая у меня была по задним боковинам — это отсутствие креплений к раме, по одному переднему креплению с каждой стороны, из-за чего пластик громыхал как не в себя.
Наращиваем площадку.

И крафтим крепление. Самый лучший вариант — это надыбать кусок АБС-пластика (или полипропилена, или любого иного, из которого у вас исходная деталь) и вырезать из него подходящую деталь. У меня такого не было, потому пришлось проявить фантазию и паять из прутков. Долго, муторно, не очень красиво, но зато пластик по итогу держится очень добротно. Толщина — полтора-два прутка, поскольку я не очень угадал с расстоянием до рамы. А так — и прочности прибавило, и обрабатывать проще.



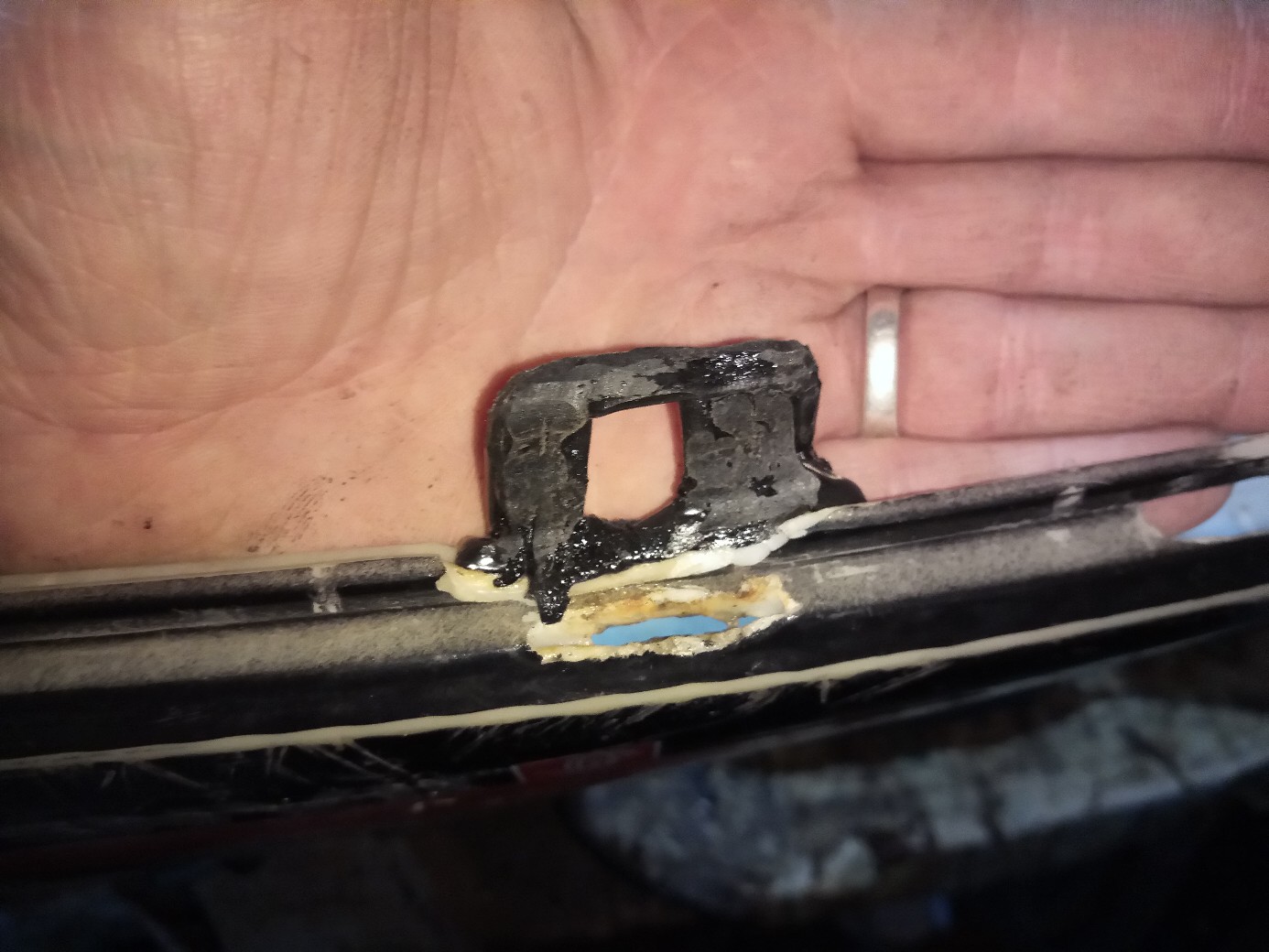

Теперь самое вкусное — кофр. Расстояния большие, всё держится одним куском — ляпота. Пропиливаем канавку и кладём шов. Повторяем пока не закроем все трещины. После чего убираем лишнее и радуемся результату.

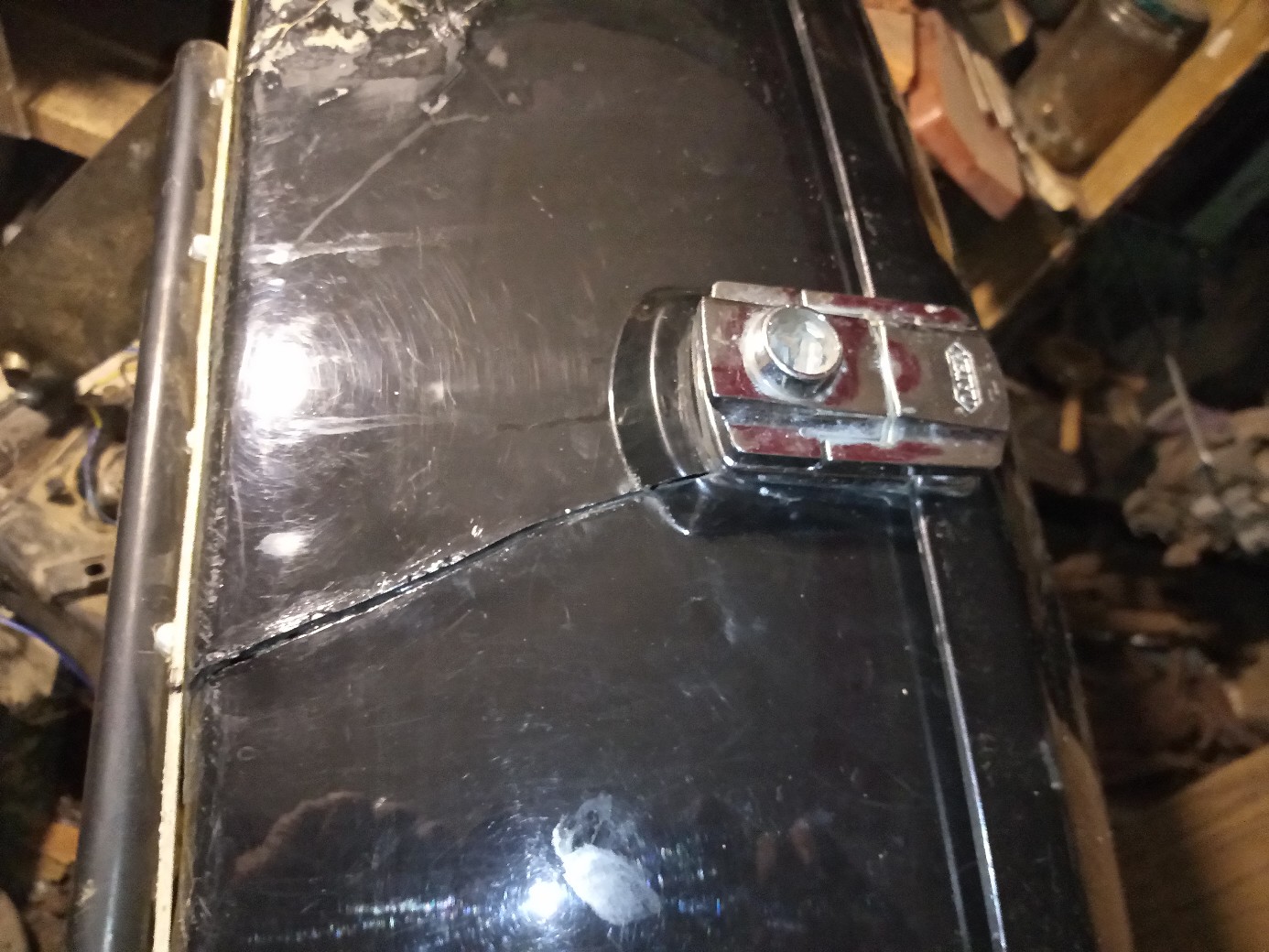



Ещё одна большая проблема — это отсутствие куска пластика на крышке кофра. Накидываем прутками нужную форму, обтачиваем — и вуа-ля, кофр становится почти как новенький.

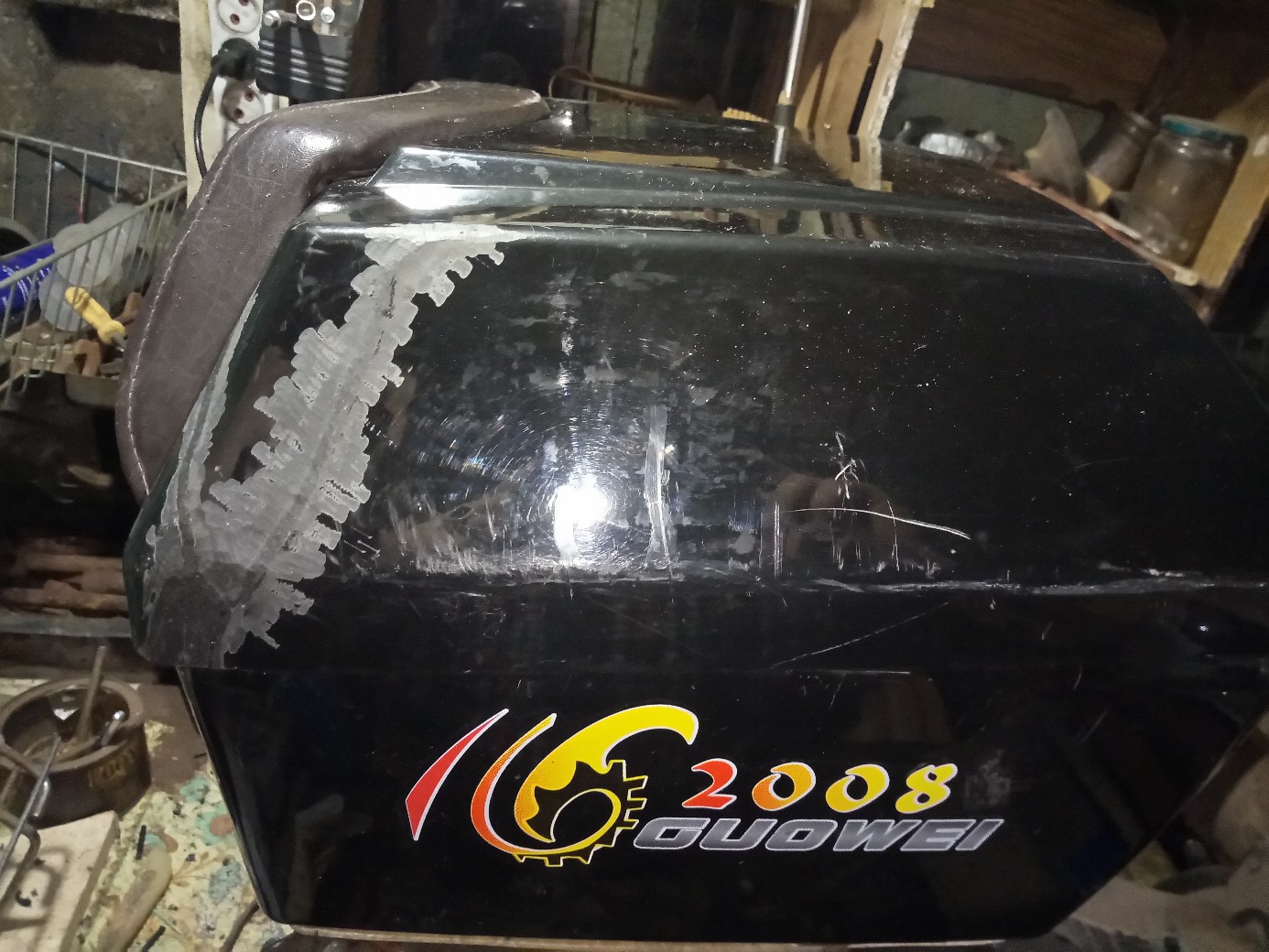
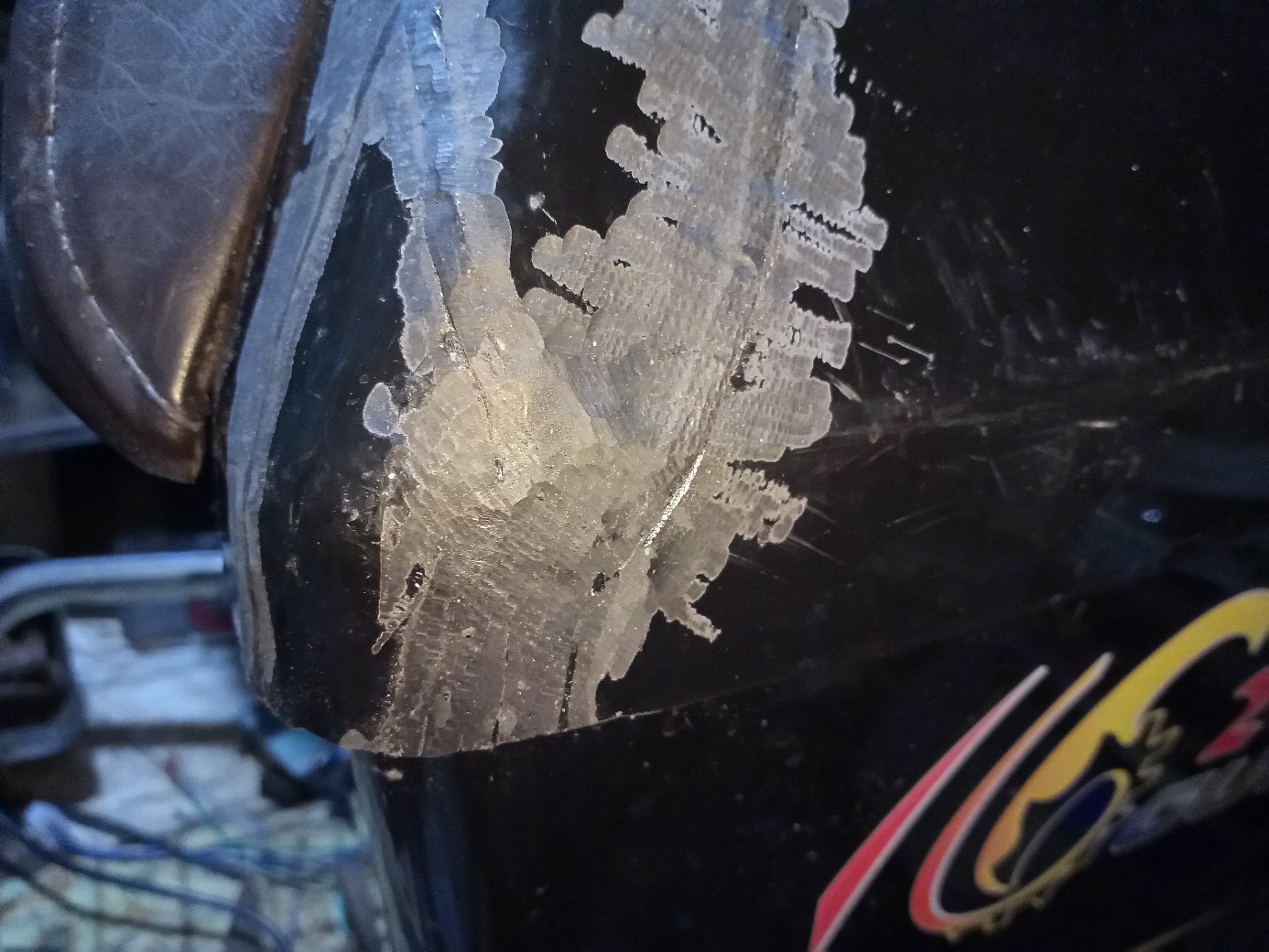

Единственное, что меня достаточно сильно напрягло — это то, что кофр был проварен только по наружной стороне. Внутри всё было пропаяно сеткой и залито эпоксидкой. Решение рабочее, но очень сильно уступает по надёжности проварке пластиком. Губить фрезы о стальную проволоку я не стал, так и оставил. Кофр никакой несущей нагрузки на себе не несёт, потому тут ничего страшного нет, но если бы были элементы несущими — пришлось бы как-то проходить трещины, дабы выкорчевать сетку.
На этом ремонт пластика у моего «Фужика» закончен. Теперь остаётся только покрыть шпаклёвкой по пластику, зачистить и прокрасить, избавившись от некошерных наклеек. Впрочем, лакокрасочные работы будут уже на следующий год. Всем удачи на дорогах.
RichardRow
- Дмитрий
- 2 октября 2018 в 13:35
- 3
- +13

- RichardRow
- 2 октября 2018 в 14:22
- ↑
- ↓
Клеить или паять — это вопрос достаточно спорный. Хотя я лично склоняюсь именно к пайке пластика. Да, тонкий пластик, как у меня на решётке, его можно и проклеить, даже, наверное, и лучше будет проклеить. Однако восстанавливать крепления и силовые элементы поклейкой я вот как-то не рискну. К тому же при наличии одних только паяльных прутков (хоть фирменных типа Фулена, хоть нарезанных из бамперов) можно восстановить крепление или заделать дыру в пластике, а вот для склейки придётся искать из чего детальку/крепление делать. В соотношении цена/качество — лично для меня пайка выглядит лучше, но она требует наличия инструмента, который не настолько и дёшево (хотя и не так чтобы и дорого) стоит. Ну и главный аргумент для меня в пользу пайки — у меня уже всё в наличии для неё есть, а для склейки — надо покупать/заказывать этот самый дихлорэтан, да и сами деталюшки надо из чего-то резать.

- RichardRow
- 2 октября 2018 в 15:53
- ↑
- ↓
А смысл указывать какие конкретно инструменты? Газовый паяльник легко заменяется паяльной станцией или термофеном с насадкой. Гравировалок на рынке тоже на любой вкус, цвет и размер, хоть аккумуляторные, хоть сетевые. Фрезы — самый обычный китайский «ноунейм» с одного известного сайта.
Газовое паяло, которым производился нагрев. Ссылка на мой обзор тут же на БайкПосте.

Фрезы что-то типа таких

Грызлик вот такого плана, только другой марки.
Газовое паяло, которым производился нагрев. Ссылка на мой обзор тут же на БайкПосте.

Фрезы что-то типа таких

Грызлик вот такого плана, только другой марки.
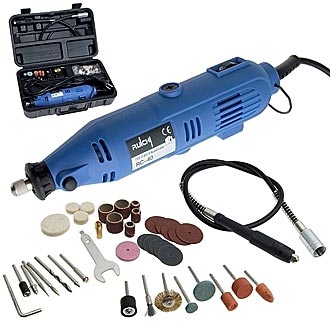

Берем абс нужного цвета… Кромсаем на мелкие кусочки… Заливаем ацетоном… Ждем (ночь в среднем)…
Полученной густой пастой с помощью медицинского шприца наносим, даем просохнуть… Единственный минус — сонет долго (ту же ночь в тепле) Но склеивает намертво, без перегрева пластика и других минусов склейки паяльником.
Полученной густой пастой с помощью медицинского шприца наносим, даем просохнуть… Единственный минус — сонет долго (ту же ночь в тепле) Но склеивает намертво, без перегрева пластика и других минусов склейки паяльником.

- RichardRow
- 2 октября 2018 в 16:37
- ↑
- ↓
Способ хорош, но не для силовых конструкций. Боюсь, силовые части пластика, те же крепления, могут и поотлетать, чего не случается при правильной пайке. Плюс ко всему, пластик на мотоциклах не только ABS, но ещё и PP (полипропилен) и PE (полиэтилен), а такой фокус для них может и не прокатить.

Для них — точно не прокатит :) Это для абс-а, да…
А крепления и пр. — если получится задать форму и пр. — будет держать лучше пайки… Единственный минус — пластичность этого «клея»… Пока не высохнет…
Но по опыту — подпаиваешь редкими точками паяльником, чтобы держало форму, а потом уже проклеиваешь и оставляешь сохнуть :)
А крепления и пр. — если получится задать форму и пр. — будет держать лучше пайки… Единственный минус — пластичность этого «клея»… Пока не высохнет…
Но по опыту — подпаиваешь редкими точками паяльником, чтобы держало форму, а потом уже проклеиваешь и оставляешь сохнуть :)

- RichardRow
- 2 октября 2018 в 16:44
- ↑
- ↓
Надо будет попробовать такую штуку провернуть с кофром, в качестве шпаклёвки его там накидать. Да и вообще по всем неровностям и косякам пройтись именно таким вариантом. Спасибо за наводку.

- RichardRow
- 2 октября 2018 в 17:44
- ↑
- ↓
У меня выхлоп регулируется рычажком на корпусе, Dremel — там у него своя крутилка. Насчёт других — не могу сказать. Как измерять — можно, например, пирометром при нагревании материала. Лично я регулировал по скорости плавления материала, дабы не перегревать и более-менее комфортно работать.

- RichardRow
- 2 октября 2018 в 19:20
- ↑
- ↓
Примерно после пары-тройки часов пайки уже примерно понимаешь как должен вести себя пруток и подстраиваешься под него. Лично для меня этот процесс скорее интуитивный, нежели какой-то научный и как-то обоснованный. Нагреваешь — плавишь — ведёшь — получаешь результат. Вот только для аккуратного шва придётся долго и нудно учиться, поскольку простота оборудования и процесса требуют достаточно продвинутого скилла.

- AntonKatenev
- 2 октября 2018 в 22:22
- ↓
Это не пайка — это сварка. Лучше делать ее специальным электрическим феном с насадкой под сварочный пруток, будет быстрее и аккуратнее. А вообще хороший способ, лучше склейки, все это примерно аналогично сварке металла. Многие пластиковые конструкции так и делают, особенно из листового пластика. Емкости всякие, септики, и так далее. Если все правильно подобрано и сделано, будет не хуже нового по прочности.

- RichardRow
- 3 октября 2018 в 7:57
- ↑
- ↓
Этот термофен с насадкой ещё найти и заказать надо. Тем более не везде сварочная насадка будет к месту. Варить большие объёмы — это да, тут она вне конкуренции, однако для мототемы больше подходит именно такой вариант с паяльником или термофеном с узким выходом. Восстанавливать крепления и различные сложные конструкции — тут вообще насадка не поможет.
P.S. по гайдам сие творчество называется пайкой. На конкретике не настаиваю ))
P.S. по гайдам сие творчество называется пайкой. На конкретике не настаиваю ))

- AntonKatenev
- 3 октября 2018 в 14:37
- ↑
- ↓
Если используется материал с такой же температурой плавления, как и у основного, и прочность достигается за счет сплавления — это сварка. Если температура плавления ниже, и прочность за счет адгезии — это пайка. Все как с металлами. Но из-за того, что при сварке пластиков часто используют паяльное оборудование по металлу — есть определенная путаница в терминологии.
Вот тут много чего есть по теме: топик на чипмейкере
Вот тут много чего есть по теме: топик на чипмейкере

- RichardRow
- 3 октября 2018 в 14:52
- ↑
- ↓
Благодарю за наводку на информацию, хотя вся теория уже изучена и активно применяется на практике. Для таких работ решает уже не теория, которой не особо много и есть, а уже сам навык работы по материалам.

- AntonKatenev
- 3 октября 2018 в 15:23
- ↑
- ↓
Да, с пластиками конечно проще, чем с металлом, изучать особенно нечего. Навык тоже проще приобретается, пластик прощает ошибки. Вообще, весьма полезное умение, тем более что дорогого и сложного оборудования не нужно.
Кстати, если есть возможность, есть смысл заменить электрическую шлифку на пневму с оборотами тысяч на 60. Будет в разы удобнее и точнее при разделке шва. Она недорогая, но компрессор нужен с очень приличной производительностью.
Кстати, если есть возможность, есть смысл заменить электрическую шлифку на пневму с оборотами тысяч на 60. Будет в разы удобнее и точнее при разделке шва. Она недорогая, но компрессор нужен с очень приличной производительностью.

- RichardRow
- 3 октября 2018 в 15:38
- ↑
- ↓
А вот тут я очень сильно поспорю. Мне удобнее вообще на самой маленькой скорости работать — тогда фрезы именно прорезают пластик. На высоких оборотах даже фрезы под пластик его начинают плавить. Так что тут мне удобнее электрой с невысокими оборотами.
Насчёт металла — там тоже ничего сверхординарного нету. Особенно при работе полуавтоматом. Разве что уже требуется стоящее денег оборудование.
Насчёт металла — там тоже ничего сверхординарного нету. Особенно при работе полуавтоматом. Разве что уже требуется стоящее денег оборудование.

- AntonKatenev
- 3 октября 2018 в 16:06
- ↑
- ↓
Варить чернину полуавтоматом, особенно с синергией — ничего сложного. Сложности начинаются, когда TIG, алюминий, нержа, титан и тому подобное.
В этой шлифке нет высоких оборотов, есть средние. Они как раз для пластика не подходят. А на низких теряется точность работы. Нужные именно высокие, от 50 тысяч. Тогда он легко и быстро срезает, плавиться не успевает при этом.
В этой шлифке нет высоких оборотов, есть средние. Они как раз для пластика не подходят. А на низких теряется точность работы. Нужные именно высокие, от 50 тысяч. Тогда он легко и быстро срезает, плавиться не успевает при этом.

- RichardRow
- 3 октября 2018 в 16:14
- ↑
- ↓
Ну в гаражном ремонта востребована сварка алюминия и нержи, всё остальное — уже сильно разовые случаи. «Аргонить» алюминий — там тоже нет ничего сверхординарного. Нержа в принципе и обычным инвертором варится, по крайней мере у меня оно варилось (хотя и электроды были специальные). С другой стороны лично у меня большой потребности в сварке чего-то кроме «чернухи» в принципе нету.
Насчёт шлифмашинки — я как-то насобачился именно на низких работать. Мне как-то оно комфортнее и удобнее. Не исключаю, что я делаю неправильно что-то, но вся пайка/сварка/токарка у меня познаётся исключительно самообразованием. Ну и чем-то делюсь с окружающими. Как минимум собственный опыт пополнить )))
Насчёт шлифмашинки — я как-то насобачился именно на низких работать. Мне как-то оно комфортнее и удобнее. Не исключаю, что я делаю неправильно что-то, но вся пайка/сварка/токарка у меня познаётся исключительно самообразованием. Ну и чем-то делюсь с окружающими. Как минимум собственный опыт пополнить )))

- AntonKatenev
- 4 октября 2018 в 11:23
- ↑
- ↓
Нормально варить алюминий — уже нужен приличный TIG с переменкой, и хороший навык. Серьезных сложностей как правило нет, но это конечно не в чернину полуавтоматом тыкать. Мне пришлось повозиться, пока добивался нормального результата. Кстати сильно помогла смена горелки на хорошую американскую, и газовые линзы. С нержой свои заморочки, но они больше связаны с режимами и правильной подачей газа куда надо (если хочется действительно аккуратно и качественно). Титан варился без особенных проблем.
На низких оборотах шлифку уводит. На высоких все идет вообще без усилий. Просто снимаешь тонкими слоями, и все. И водичкой поливать надо не забывать, по сухому лучше не шкрябать.
Говорят, такие детали хорошо варить ультразвуком, но никогда не пробовал. Серьезной работы по ремонту у меня нет, а ради баловства покупать ультразвук как-то не хочется…
На низких оборотах шлифку уводит. На высоких все идет вообще без усилий. Просто снимаешь тонкими слоями, и все. И водичкой поливать надо не забывать, по сухому лучше не шкрябать.
Говорят, такие детали хорошо варить ультразвуком, но никогда не пробовал. Серьезной работы по ремонту у меня нет, а ради баловства покупать ультразвук как-то не хочется…

- RichardRow
- 4 октября 2018 в 13:25
- ↑
- ↓
За хорошее оборудование согласен. Для действительно хорошей сварки металлов придётся раскошеливаться. Скорее всего, когда-нибудь приду и к такому оборудованию.
Не знаю, у меня фрезы вполне хорошо шли их никуда вообще не уводило, исключая моменты, когда приходилось раскорячиваться с держанием детали, подлезанием и резом по трещине. Пока всё в одни руки делается.
Насчёт ультразвука надо будет почитать, хотя не факт что буду пользоваться. Не тот у меня уровень )))
Не знаю, у меня фрезы вполне хорошо шли их никуда вообще не уводило, исключая моменты, когда приходилось раскорячиваться с держанием детали, подлезанием и резом по трещине. Пока всё в одни руки делается.
Насчёт ультразвука надо будет почитать, хотя не факт что буду пользоваться. Не тот у меня уровень )))

- RichardRow
- 3 октября 2018 в 15:49
- ↑
- ↓
Берётся пластиковая пластинка, как на кофре (если АБС — то бампер/колёсный колпак, если ПП — то можно попробовать с «фикса» поискать), берутся прутки для пайки (лучше покупные, но можно и самому нарезать), берётся газовый паяльник/термофен — и можно работать. Пластинка нужна для укрепления силового элемента крепления петель. Можно, конечно и прутками изобразить, но пластинка будет лучше. У меня такое «фигурное творчество» из-за отсутствия пластинок.
Конкретику надо смотреть по месту, но сложного вообще ничего нет.
Конкретику надо смотреть по месту, но сложного вообще ничего нет.

- EvgeniyPopov
- 4 октября 2018 в 10:57
- ↓
А не проще с таким обьемом работ раздеть до нейкеда? Хотя ответ и так понятен, дай бог, чтоб держалось

- RichardRow
- 4 октября 2018 в 11:07
- ↑
- ↓
Максискутер в нейкед? Это уже что-то новенькое, если честно…
Объём работ, по факту выполнения, не такой и большой и не особенно сложный. Да, швы тут длинные, но пластик из битых компонентов не пришлось восстанавливать, потому сложностей минимум — паяй себе в удовольствие и всё.
Объём работ, по факту выполнения, не такой и большой и не особенно сложный. Да, швы тут длинные, но пластик из битых компонентов не пришлось восстанавливать, потому сложностей минимум — паяй себе в удовольствие и всё.

- EvgeniyPopov
- 7 октября 2018 в 10:42
- ↑
- ↓
Я после армии на своей Тулице " потерял 2-ю в коробке" и после колки мотора как то не захотел вешать корыто обратно. Уж не знаю, понятливые, зачтете за ответ?
PS. капот был цел, свеж, но тяжел
PS. капот был цел, свеж, но тяжел

- RichardRow
- 7 октября 2018 в 12:02
- ↑
- ↓
Эмм… «Тулица» — это «Тулица», у неё из пластика только декоративные элементы, которые ещё попробуй оторвать. Любой современный скутер состоит полностью из пластика по наружке и в варианте «нейкед» мало того что вид… скажем так ужасный, так ещё и наружу очень много того, что нежелательно замочить.
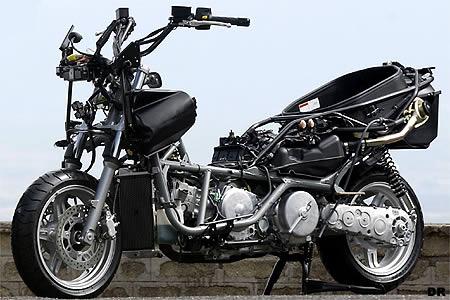
P.S. «Бург» 650 в варианте «нейкеда». как по мне — видок ну очень не очень.
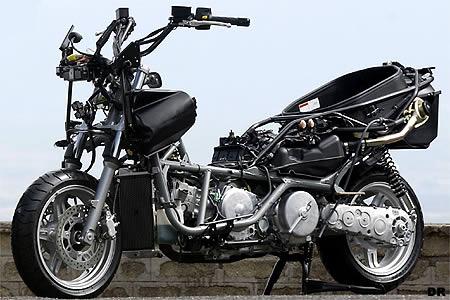
P.S. «Бург» 650 в варианте «нейкеда». как по мне — видок ну очень не очень.
Только зарегистрированные пользователи могут оставлять комментарии.
Войдите, пожалуйста, или зарегистрируйтесь.
Комментарии (29)
RSS свернуть / развернуть