Блог им. Sergusster → Продвинутый колхоз: от идеи до воплощения, первый опыт.
Сей пост может быть интересен и полезен тем, в ком, как и во мне, прозябает мамкин инженер, периодически ищущий выход своим гениальным идеям, но не имеющий необходимой базы технических знаний. Здесь я в достаточно мелких подробностях опишу как и зачем я взялся за проектирование замысловатой детали для своего мотоцикла и какой ценный опыт я получил в процессе. Кому интересно, милости прошу под cut :)
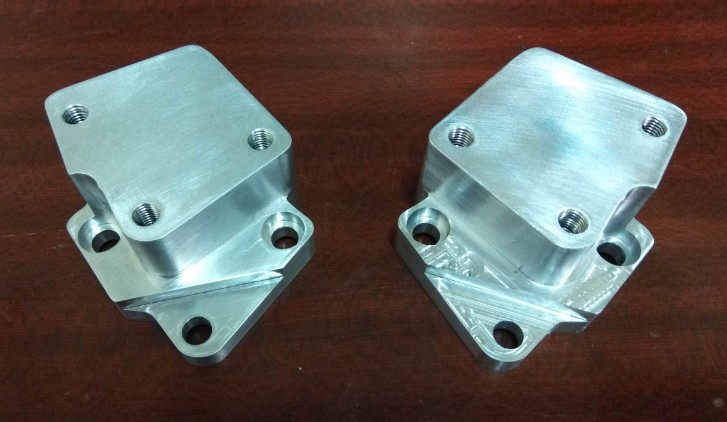
Решение подобной проблемы, конечно же, давно придумано человечеством – т.н. проставки стоек руля (англ. handlebar risers), приподнимающие руль и, соответственно, делающие его немного ближе к райдеру. Для многих популярных моделей мотоциклов такие детали выпускаются на рынке тюнинга, а иногда и самими производителями. Тем паче, что у большинства мотоциклов руль представляет собой круглую трубу, зажатую двумя незамысловатыми «скобками», прикрученными к верхней траверсе.
Мне же с моим маленьким китайцем «повезло» вдвойне. Во-первых, как и у многих больших и серьезных одноклассников, руль представляет собой два «рога» приболтованных к траверсе. Подобные крепления не стандартизированы даже от модели к модели, не то что между производителями, поэтому традиционные проставки автоматически отпадают.
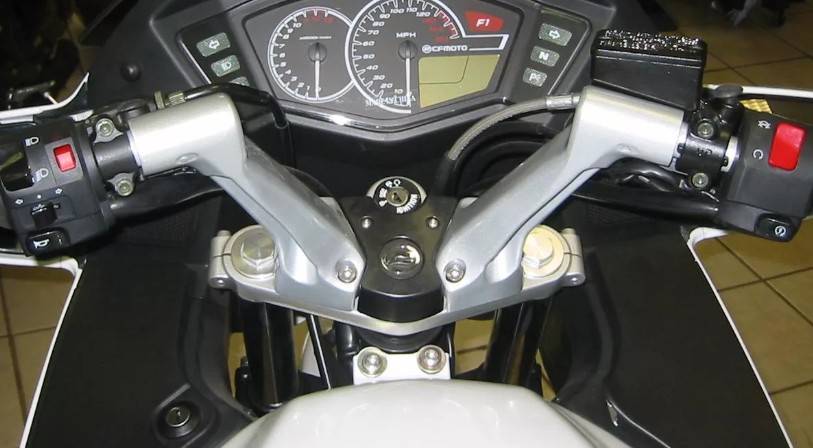
Во-вторых – модель моего мопеда не очень популярна даже среди поклонников техники CFMOTO, поэтому, ожидаемо, тщательное гугление готовых наработок не дало никаких результатов.
Ну, что ж, если нужной детали не существует, значит её надо придумать и сделать :)
Для начала разработки, необходимо снять размеры оригинальных деталей. В частности — руля. Для этого один из «рогов» был демонтирован и принесён домой. Выглядит он вот так.
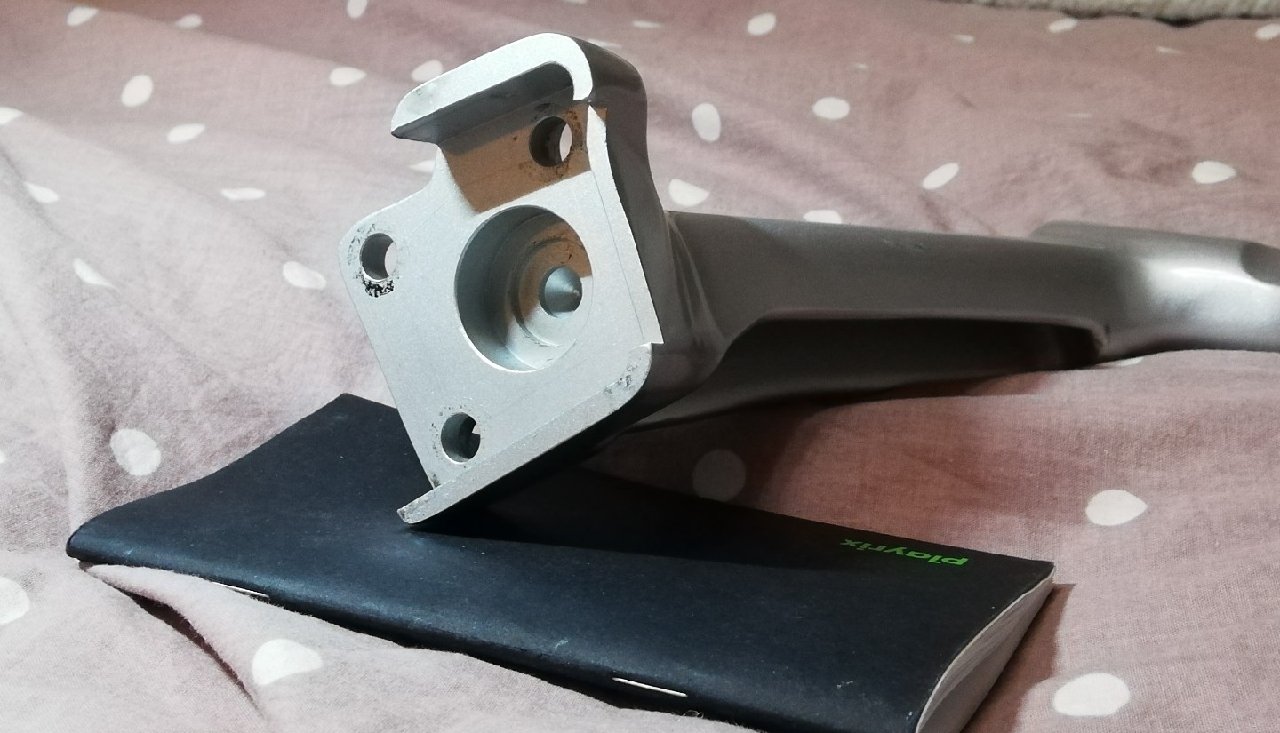
Понятно, что такую фиговину просто к бумажке не приложишь и маркером не обведешь. Самым эффективным, на мой взгляд, решением было бы 3D сканирование детали. Но профессионального 3D сканера у меня под кроватью, увы, не завалялось. Прочие занятные идеи, мелькавшие у меня в голове, такие как создание слепка или отпечатка профиля или даже сканирование обычным сканером для документов я довольно быстро отмёл из-за потенциально высокой погрешности в полученных размерах. Самым доступным подручным методом оказалась старая добрая фотограмметрия: метод построения геометрии реального объекта в трёхмерном пространстве, путём хитрого сличения контрастных областей в ряде изображений объекта. Иными словами — фотографируем неподвижный объект с как можно большего количества ракурсов, загоняем фотографии в специальную программку, нажимаем кнопку (иногда две) и через некоторое время получаем трёхмерную модель.
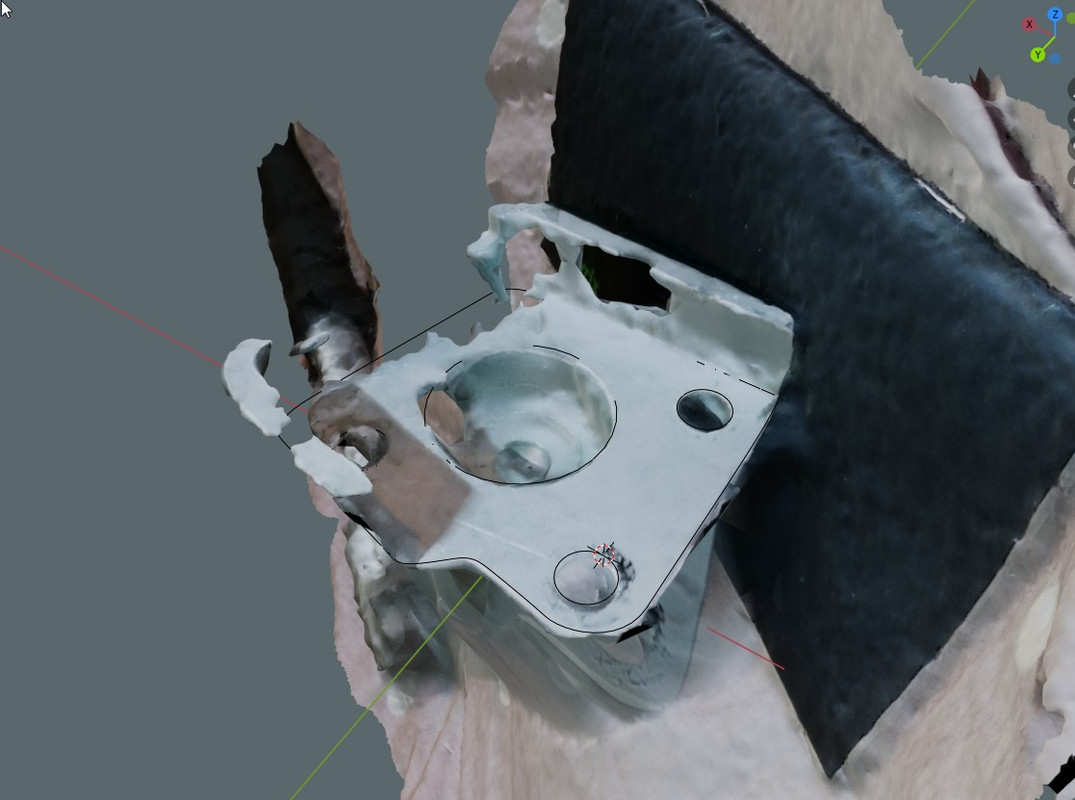
Да, домашняя фотограмметрия не даёт супер-результатов, чистой геометрии и реальных размеров детали, но главная цель — получение относительных размеров, достигнута. Теперь нужно точно знать всего один размер, например, одного из отверстий или одной из сторон периметра (если у детали есть прямые грани), чтобы по нему подогнать 3D модель к реальному масштабу.
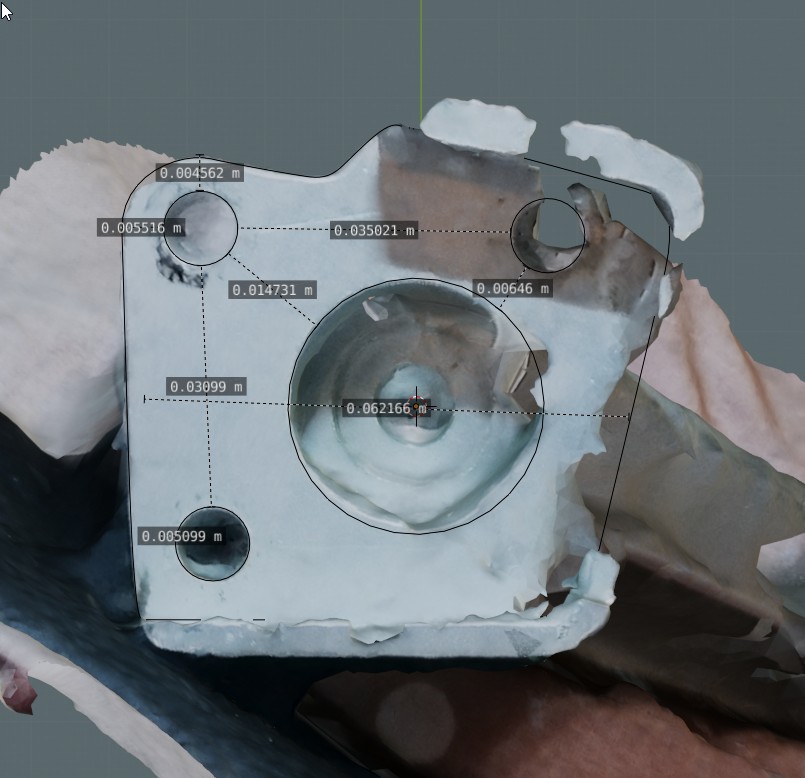
Теперь остается вручную построить кривую профиля, расположить отверстия/углубления и voilà — основной профиль готов.
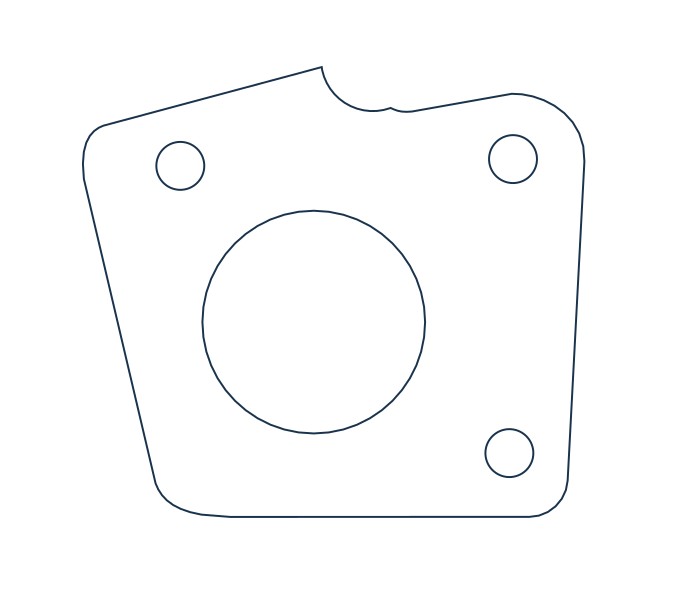
Перед дальнейшей работой над деталью, нужно убедиться что кривизна детали и все размеры сняты правильно. Для этого из обычной фотобумаги на плоттере вырезается вот такая штуковина и прикладывается в рулю. Если всё «попало», можно двигаться дальше.
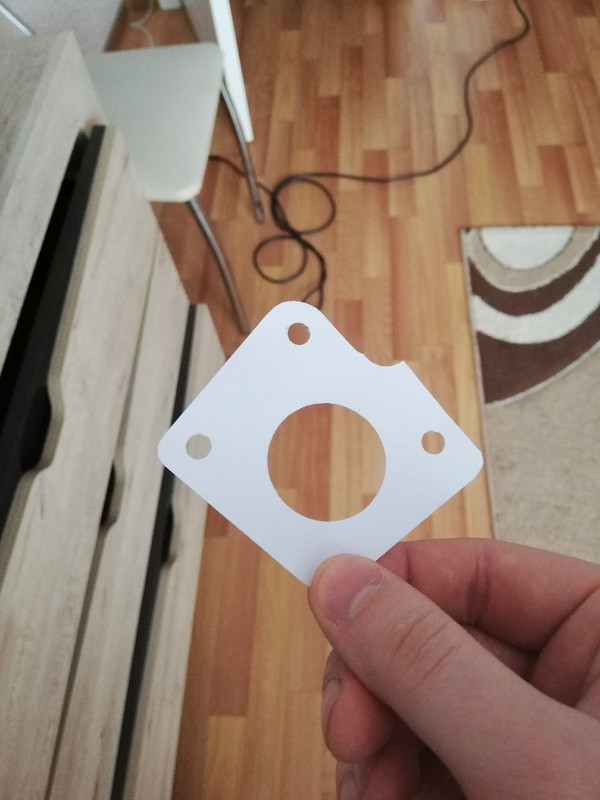
Столь прямолинейное решение было отвергнуто по двум причинам: 1) особенность оригинальной конструкции, заключавшаяся в декоративной пластиковой заглушке с логотипом, прикрывавшей один из трёх болтов, крепящих руль и заглушку оси рулевой колонки; 2) вероятность ухудшить обзор в зеркалах, просто подняв руль (т.к. зеркала находятся на корпусе мотоцикла, ниже уровня грипсов)
И если с потерей декоративной заглушки ради комфортной посадки иной райдер ещё может смириться (хотя я категорически не хотел), то ухудшение обзора абсолютно неприемлемо.
Так родилась идея сделать площадку, с… ещё одной площадкой под руль, смещённой относительно оригинальной нормали и немного наклонённую на райдера. Чтобы лучше представлялось, забегая вперед покажу одну из первых итераций детали.
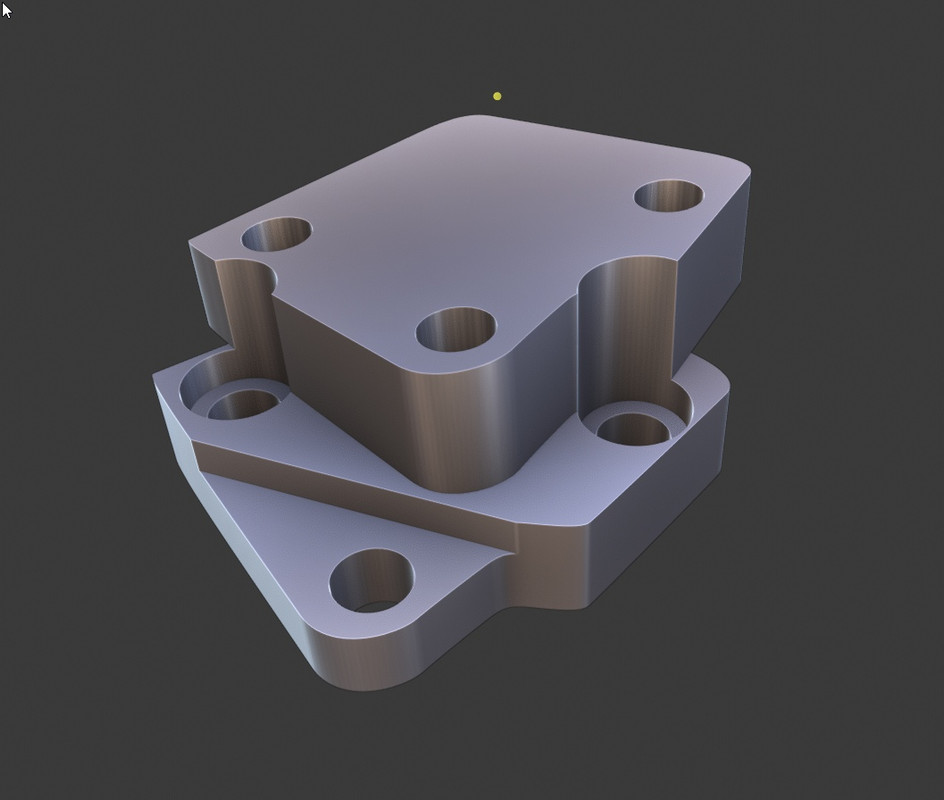
Профессия моя никак не связана с чертежной или проектировочной деятельностью, поэтому этап создания чертежа я пропустил и сразу приступил к созданию 3D модели. Благо с компьютерной графикой моя профессия связана напрямую, этот этап был самым простым и предсказуемым. Для создания модели я выбрал софт, в котором работаю каждый день — Blender 3D и аддон (плагин) Sverchok, для параметрического моделирования. Кто не знаком с нюансами, кратко поясню — параметрическое создание модели означает, что в противовес классическому «ручному» моделированию, геометрия генерируется на основе вводимых параметров и координат, в не деструктивной манере (т.е. на любом этапе создания геометрии любой параметр можно отредактировать и вся модель пересчитается заново). Такой подход позволил быстро и безболезненно вносить изменения в последующие итерации детали.
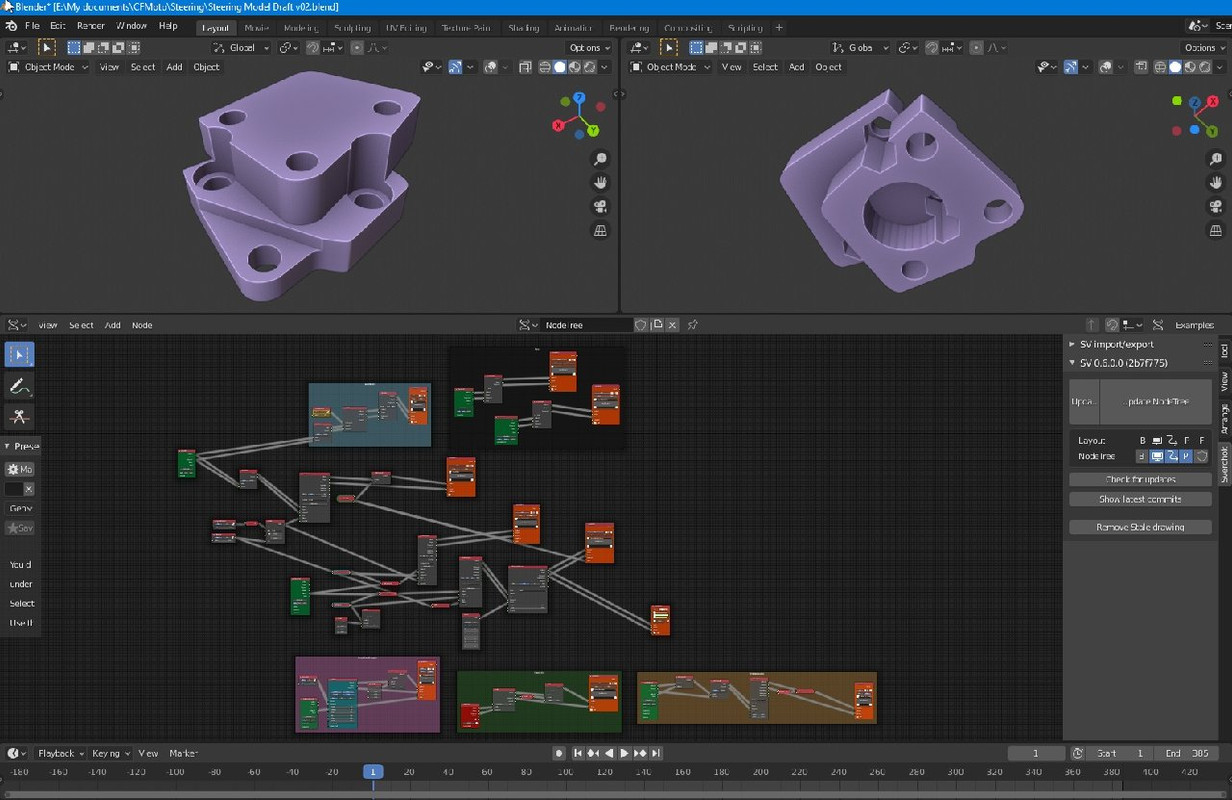
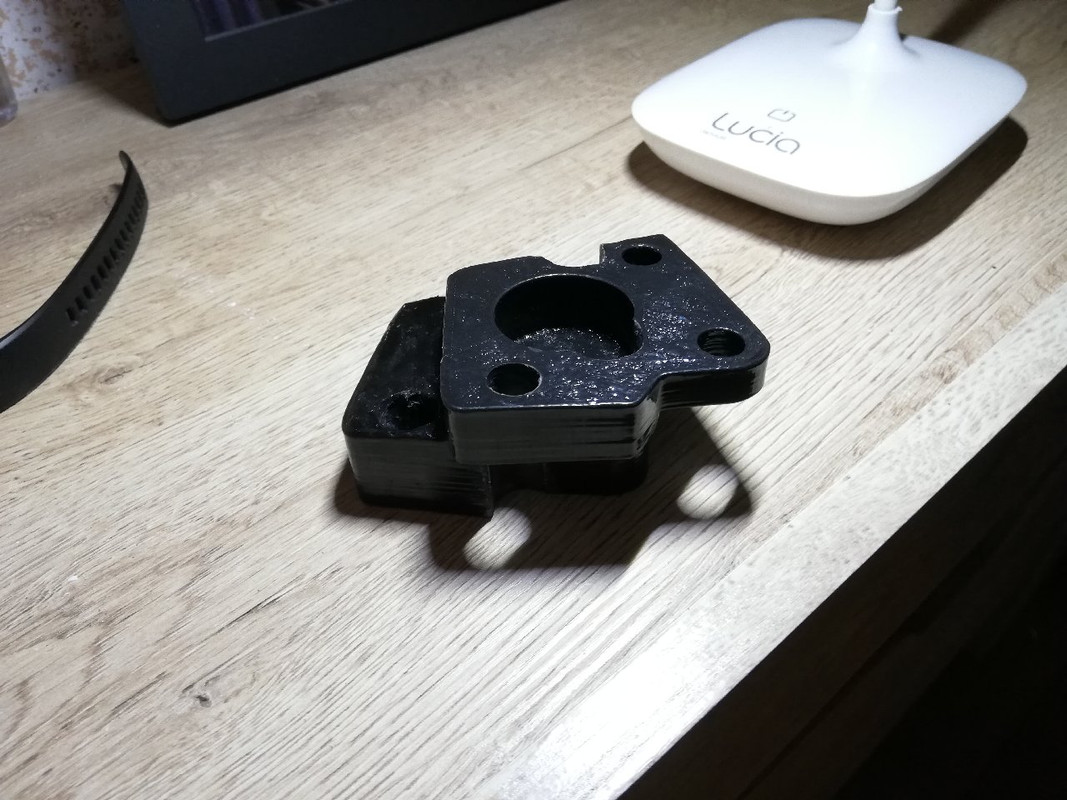
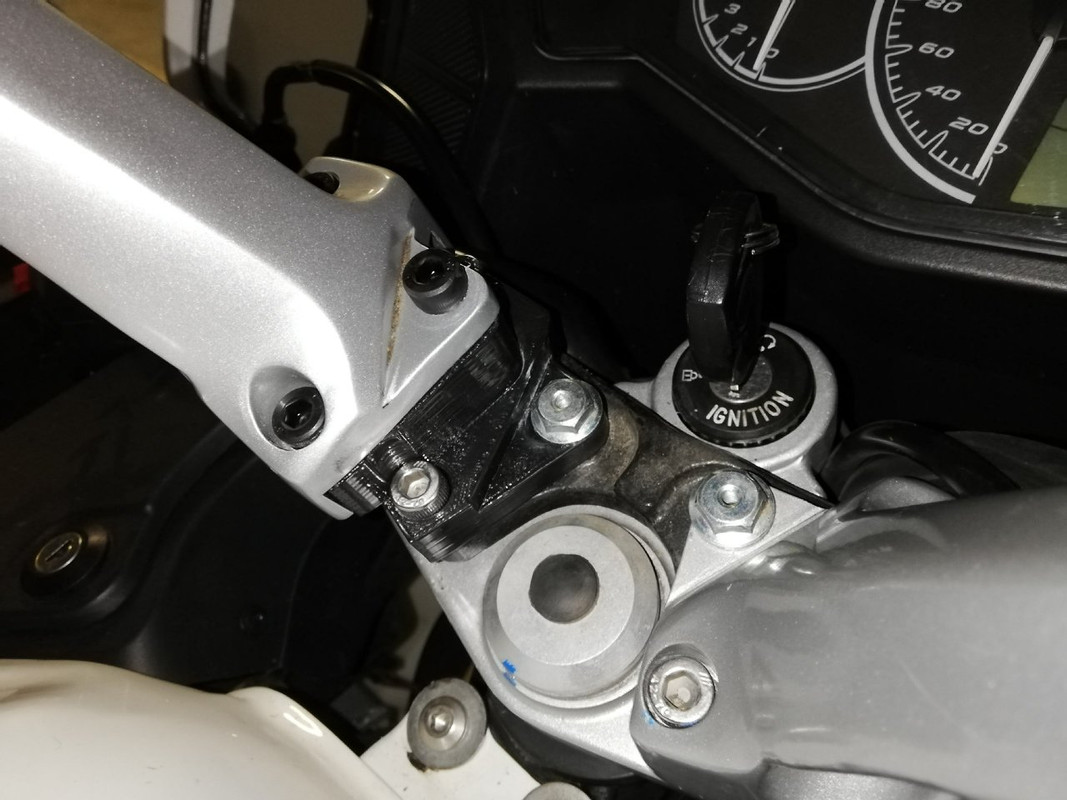
Окрылённый успехом, я незамедлительно начал поиски производства, на котором мою деталь, наконец, воплотят в благородном металле… ну, или, хотя бы в алюминии. Вот тут и дала о себе знать моя нехватка знаний в смежной области :) Первая моя ошибка заключалась в святой уверенности в том, что куда ни плюнь — попадешь во фрезерный станок с ЧПУ. Это ВНЕЗАПНО! оказалось не так. Найти станок (с грамотным мастером в придачу) в моём родном городке с населением в 50 тысяч оказалось непросто. Тут вылез мой второй промах — уверенность в том, что каждое производство хранит специально для меня алюминиевый брусок нужного размера. Это тоже оказалось не так. В общем, безрезультатно пошукав помощи через знакомых знакомых, я полез строчить объявление в интернет. Благо, живём в 21 веке и доставка всего и вся из разных уголков страны нынче дело простое и доступное. Поиски в соц-сетях привели меня в паблик ВК, этакий «черный рынок» мастеров мех.обработки, халтурящих в свободное время на производственных мощностях. Я разместил объявление о найме и стал ждать. Примерно через неделю ко мне в личку постучались сразу несколько специалистов. Я подробно обрисовал им картину, показал деталь с различных ракурсов и попросил предварительной оценки бюджета и сроков. На этом этапе меня настигло самое жестокое откровение — до сих пор я (почему-то) был уверен, что на ЧПУ станке можно сделать абсолютно любую загогулину. Но и это, черт возьми, оказалась не так! :) Запоздалое изучение вопроса показало, что станки бывают трёх-, пяти-, семи- и ещё чёрт-знает-сколько-осевые. И то, что можно выполнить на одном станке, либо невозможно, либо крайне трудозатратно на другом. Моя фантазия, не ограниченная этим знанием, родила деталь как раз обладающую свойствами «невыполнимости» на самом распространённом — трёх-осевом станке. Скрепя сердце, я принялся дорабатывать и упрощать модель. В частности, пришлось избавиться от того самого наклона руля, немного приподняв его и развернув на себя по продольной оси на 3 градуса. После всех пертурбаций в работу-таки отправилась аж восьмая версия проекта.
Но и на этом препоны не кончились! Модель, будучи изготовленной в софте не заточенном под инженерное моделирование, даже конвертированная в популярные «кадовские» обменные форматы, типа .step и .iges, не годилась для составления рабочей программы ЧПУ станка. Поэтому мне, никогда ранее не работавшему с CAD софтом, не оставалось ничего, кроме как за пару вечеров разобраться с замечательным пакетом FreeCAD и практически с нуля воссоздать деталь в ней по всем канонам и правилам. Не буду скрывать, что, учитывая полное отсутствие опыта, качеством получившейся модели я был горд.
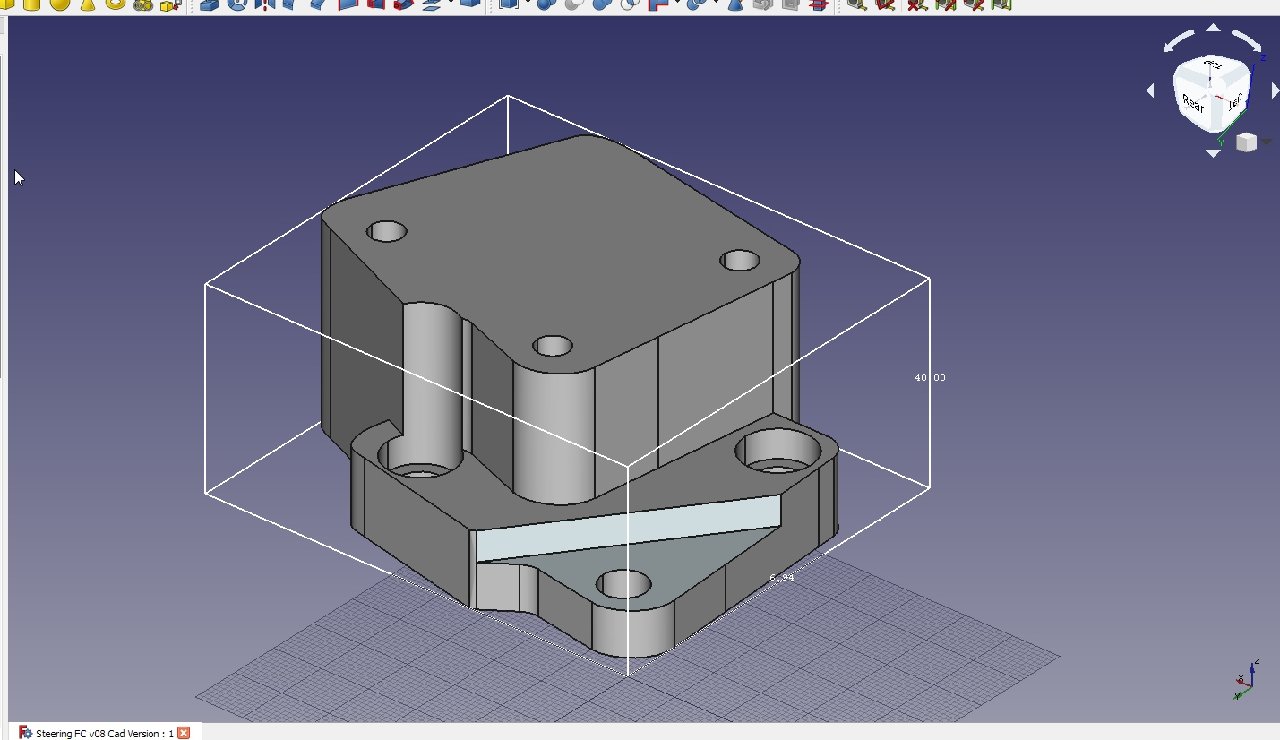
Дальнейшее общение с потенциальными исполнителями лишний раз напомнило мне о том, что такое «бизнес по-русски». Один предложил мне выточить обе детали за 10 тысяч рублей, при этом работая на ручном фрезерном станке в течении пары тройки недель :) Я не знаю, насколько он крутой мастер, но для меня так и осталось загадкой, как он собирался вручную выточить две абсолютно симметричные детали. Другой взялся за работу без лишних вопросов, за божеские 4 тысячи рублей и в недельный срок. Точил точил целый месяц, периодически извиняясь за задержки. Через месяц сообщил что обе детали, наконец, готовы и… после просьбы прислать фотографию с контрольными замерами просто перестал отвечать на сообщения :) К чему был весь этот спектакль, я так и не понял, учитывая, что я даже не делал никаких предоплат. Наконец, я всё-таки нашёл, казалось бы адекватного исполнителя по адекватной цене, да ещё и относительно недалеко от меня. Человек рассмотрел модель, уточнил некоторые нюансы, озвучил бюджет в 5 тысяч рублей и приступил к работе. Но, через полторы недели ВНЕЗАПНО! выяснилось, что изготовление требует дополнительных трудозатрат и надо бы накинуть пару тыщенок (предоплат я, опять же, не делал). Я сказал, что пару дней подумаю, но сам был настроен категорически против такого подхода. Я сам оказываю людям профессиональные услуги и в моей практике бывают сложные заказы, в процессе работы над которыми возникают неучтенные мной нюансы. Но если я перед началом работ озвучил клиенту цену, я никогда не приду к нему с просьбой добавить денег, потому что я хреново посчитал. В общем, услышав от меня отказ, мастер выполнил работу по первоначальной цене, т.к. в противном случае он просто остался бы с двумя ненужными деталями, а я бы не поленился найти другого исполнителя :)
Неделю спустя я забрал многострадальные детальки из офиса службы доставки. Вращая в руках два увесистых блестящих кусочка алюминия я дивился тому, как моя инженерная мысль сначала обрела форму на экране монитора, а затем и в реальном твёрдом металле. Чрезвычайно приятное чувство :)
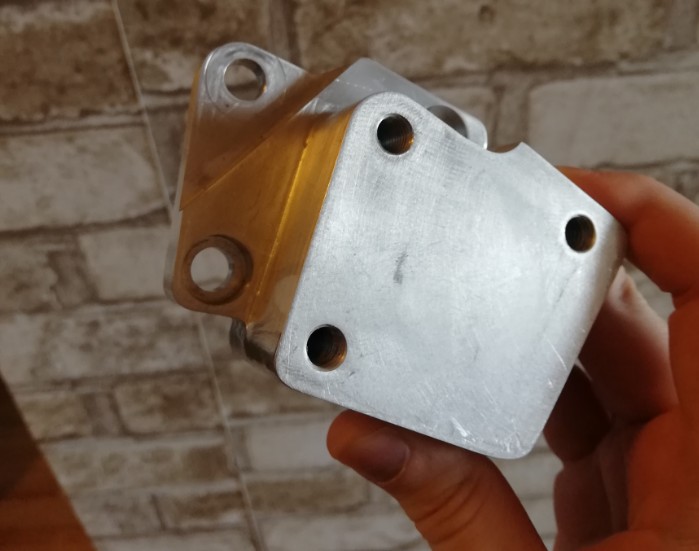
Оставалось только покрыть детали бесцветным акриловым лаком (для защиты от коррозии) и установить, наконец, на мотоцикл. Сама по себе установка заняла минут десять. В процессе я обнаружил неучтенный момент — длину электрической косы, идущей к пультам. В общем, будь проставки ещё чуть выше и все усилия вполне могли бы оказаться напрасными, т.к. встало это всё в натяг :)
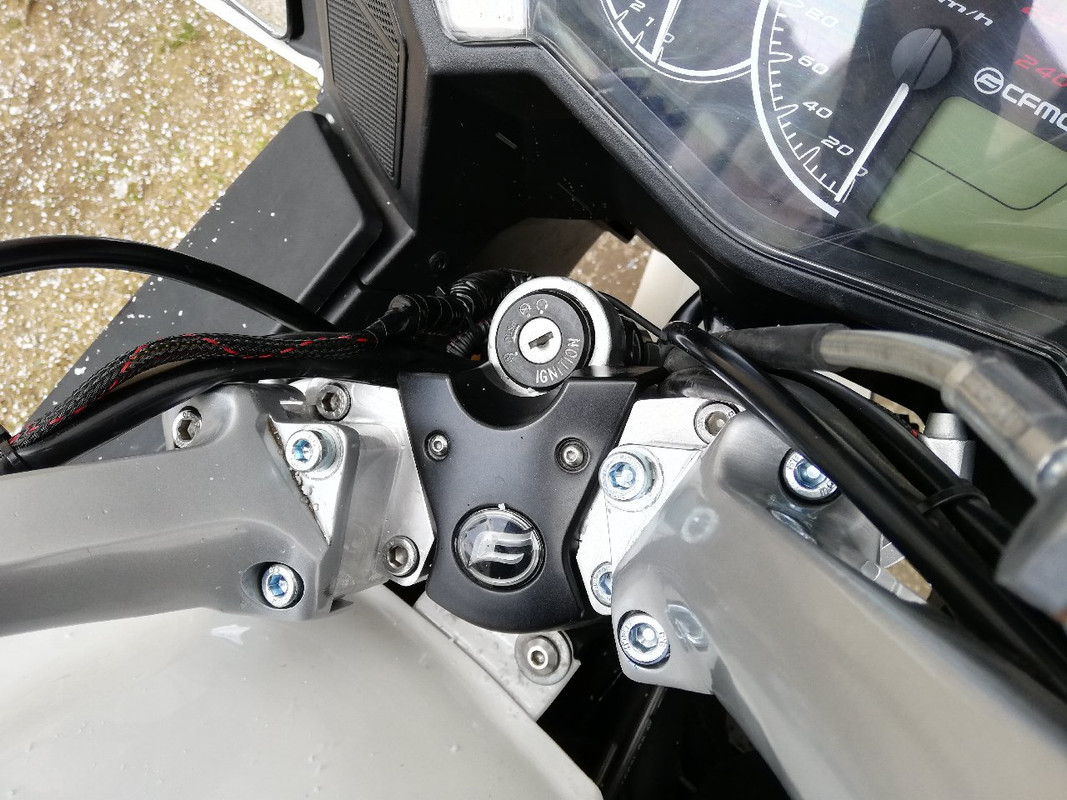
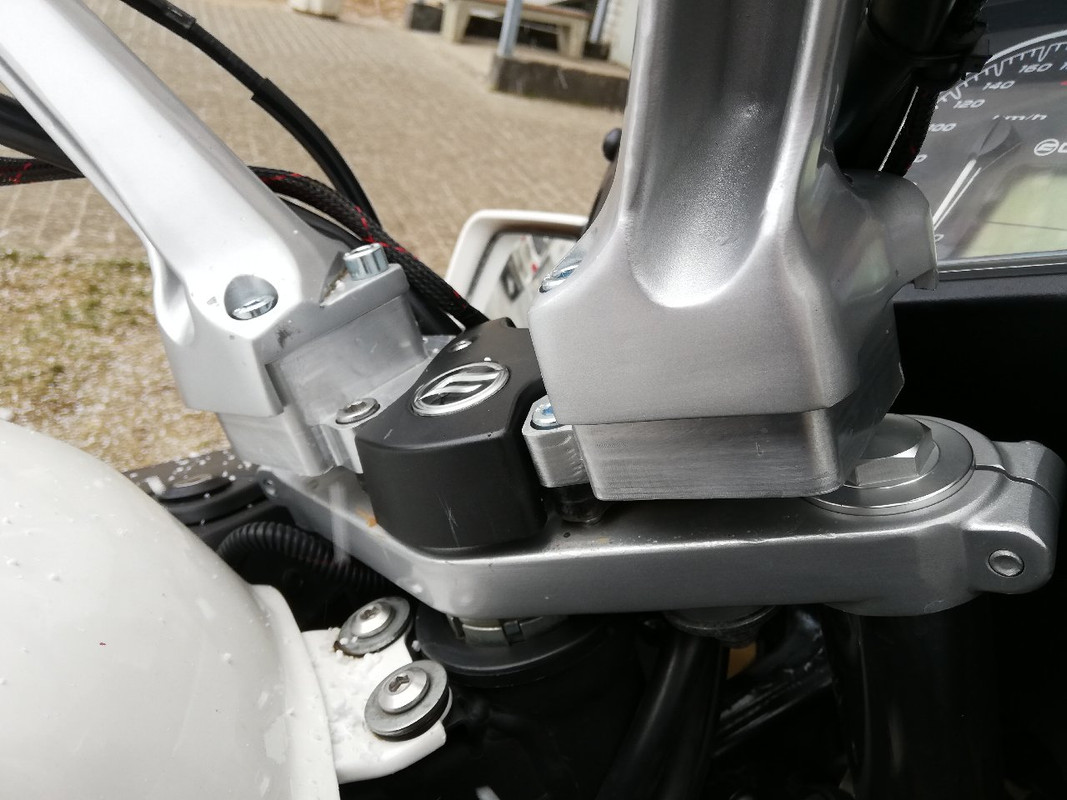
Руль стал на 37 мм выше, самую малость шире и немного развернут ко мне. Искомый эффект достигнут — посадка теперь более расслаблена, руки согнуты в локтях, запястья просто лежат на руле. Обзор в зеркала на удивление даже стал чуть лучше. Из ожидаемых минусов только изменившиеся ощущения от активной рулежки на малых скоростях, но это как раз то, чем я могу пожертвовать ради комфорта в дальней дороге.
Весь проект занял около трёх месяцев (два из которых мне вытачивали деталь) и обошелся мне примерно в 6 тысяч рублей, что, учитывая цены на подобный тюнинг для других известных мотоциклов, по-моему совсем не дорого. И, конечно, сложно переоценить количество полученного опыта и новых знаний в смежных областях.
Надеюсь, чтиво было интересным, а кому-нибудь и полезным. Спасибо, что дочитали до конца! С открытием сезона и здоровья всем! :)
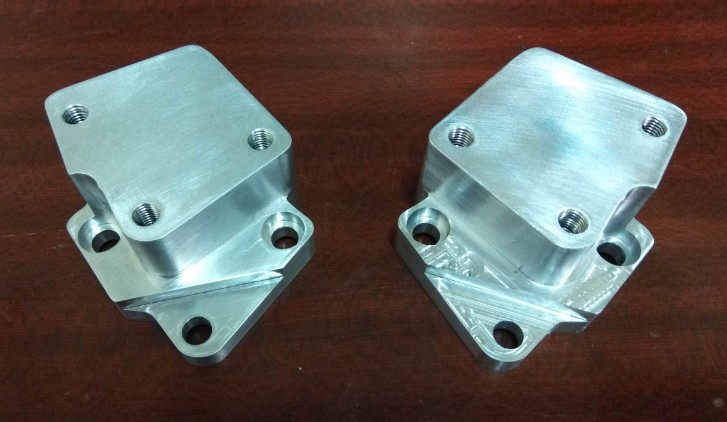
Проблематика.
Вот уже третий сезон я бесхлопотно владею небольшим спорт-турером CFMOTO 650TK. О нём я некоторое время назад писал развёрнутый отзыв после первых 14 тысяч километров на одометре, в котором, среди прочего, дал нейтрально-положительную оценку своей посадке за рулём пепелаца. Но всё течёт, все меняется, и по окончании второго сезона я всё-же пришёл к выводу что в дальних дорогах (over ~400 км за раз) посадка с прямыми руками начинает напрягать. До кучи, посидев на тур-эндурном «собрате» своего мотоцикла в куда более расслабленной позе я окончательно сказал себе «Хватит это терпеть!»Решение подобной проблемы, конечно же, давно придумано человечеством – т.н. проставки стоек руля (англ. handlebar risers), приподнимающие руль и, соответственно, делающие его немного ближе к райдеру. Для многих популярных моделей мотоциклов такие детали выпускаются на рынке тюнинга, а иногда и самими производителями. Тем паче, что у большинства мотоциклов руль представляет собой круглую трубу, зажатую двумя незамысловатыми «скобками», прикрученными к верхней траверсе.
Мне же с моим маленьким китайцем «повезло» вдвойне. Во-первых, как и у многих больших и серьезных одноклассников, руль представляет собой два «рога» приболтованных к траверсе. Подобные крепления не стандартизированы даже от модели к модели, не то что между производителями, поэтому традиционные проставки автоматически отпадают.
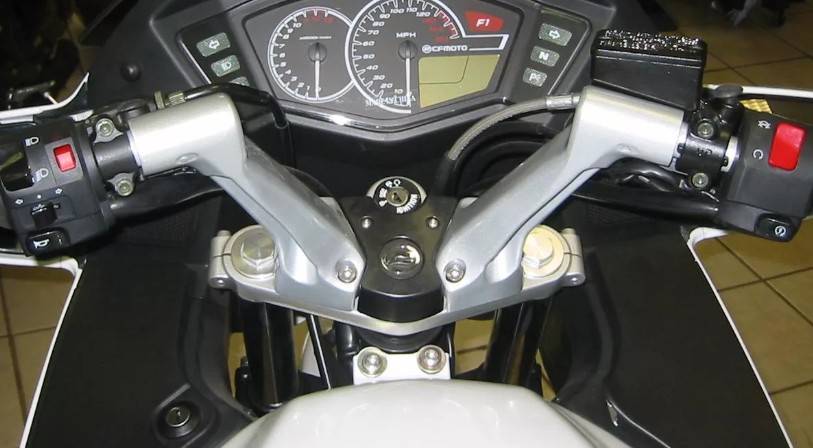
Во-вторых – модель моего мопеда не очень популярна даже среди поклонников техники CFMOTO, поэтому, ожидаемо, тщательное гугление готовых наработок не дало никаких результатов.
Ну, что ж, если нужной детали не существует, значит её надо придумать и сделать :)
Обратная инженерия.
Разумеется, сперва-наперво необходимо изучить место предполагаемой модификации, постараться учесть возможные нюансы, вызванные наличием новой детали там, где её никогда не предполагали профессиональные инженеры, убедиться что ваш «колхоз» не нанесёт (ну, или нанесёт по минимуму) ущерба эргономике и функционалу других узлов. С подобными нюансами я столкнулся практически сразу, но об этом чуть позже.Для начала разработки, необходимо снять размеры оригинальных деталей. В частности — руля. Для этого один из «рогов» был демонтирован и принесён домой. Выглядит он вот так.
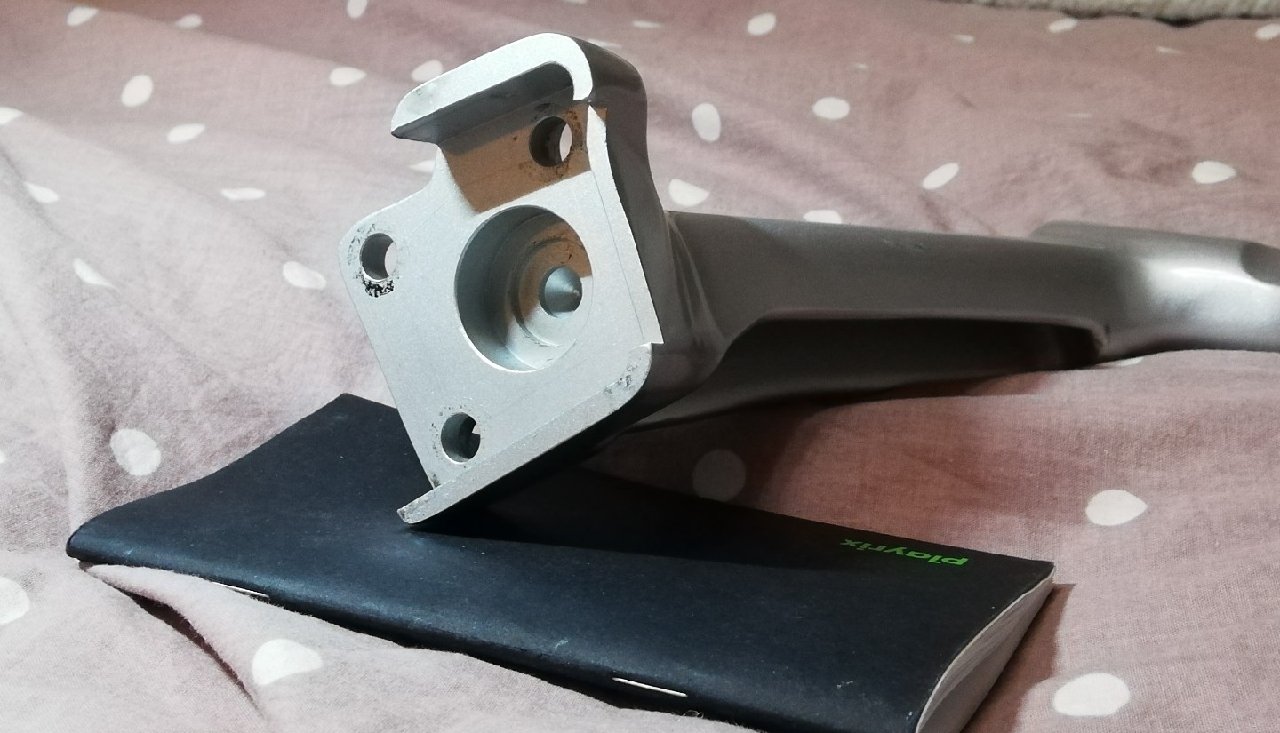
Понятно, что такую фиговину просто к бумажке не приложишь и маркером не обведешь. Самым эффективным, на мой взгляд, решением было бы 3D сканирование детали. Но профессионального 3D сканера у меня под кроватью, увы, не завалялось. Прочие занятные идеи, мелькавшие у меня в голове, такие как создание слепка или отпечатка профиля или даже сканирование обычным сканером для документов я довольно быстро отмёл из-за потенциально высокой погрешности в полученных размерах. Самым доступным подручным методом оказалась старая добрая фотограмметрия: метод построения геометрии реального объекта в трёхмерном пространстве, путём хитрого сличения контрастных областей в ряде изображений объекта. Иными словами — фотографируем неподвижный объект с как можно большего количества ракурсов, загоняем фотографии в специальную программку, нажимаем кнопку (иногда две) и через некоторое время получаем трёхмерную модель.
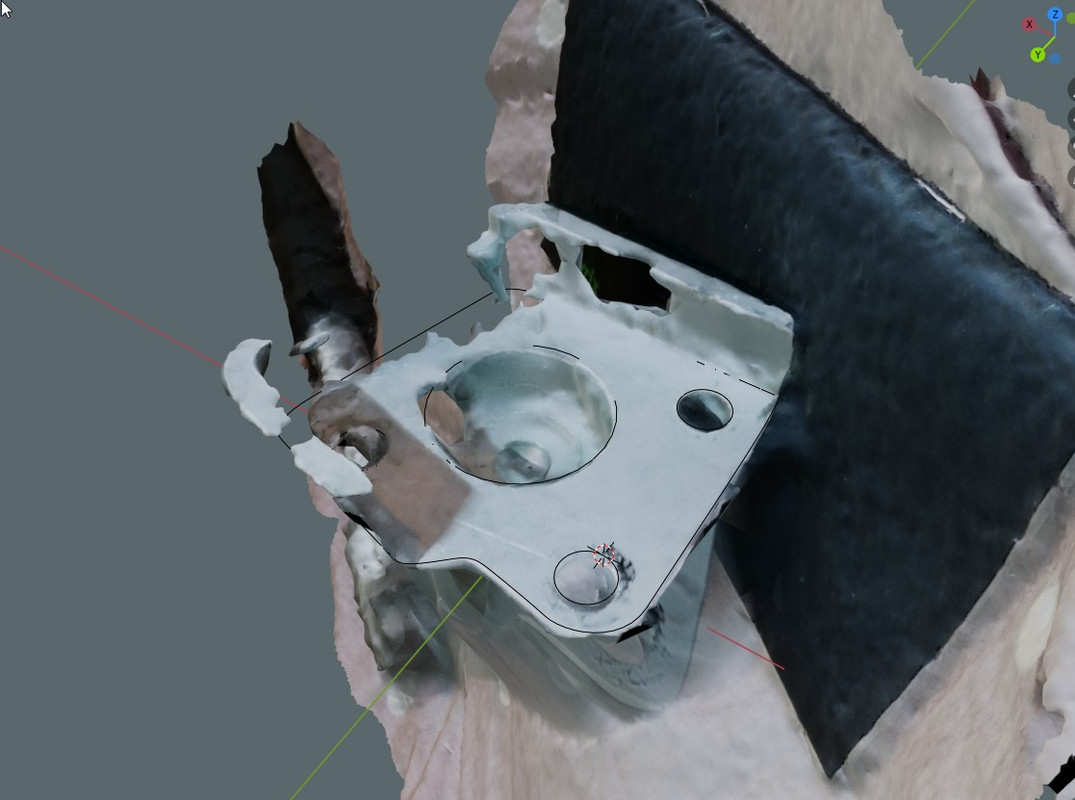
Да, домашняя фотограмметрия не даёт супер-результатов, чистой геометрии и реальных размеров детали, но главная цель — получение относительных размеров, достигнута. Теперь нужно точно знать всего один размер, например, одного из отверстий или одной из сторон периметра (если у детали есть прямые грани), чтобы по нему подогнать 3D модель к реальному масштабу.
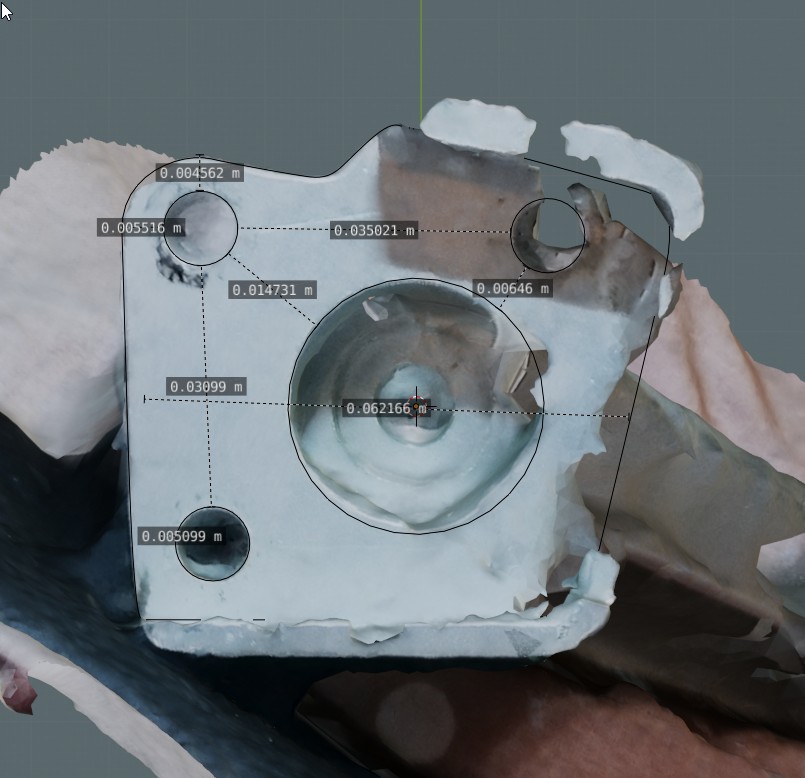
Теперь остается вручную построить кривую профиля, расположить отверстия/углубления и voilà — основной профиль готов.
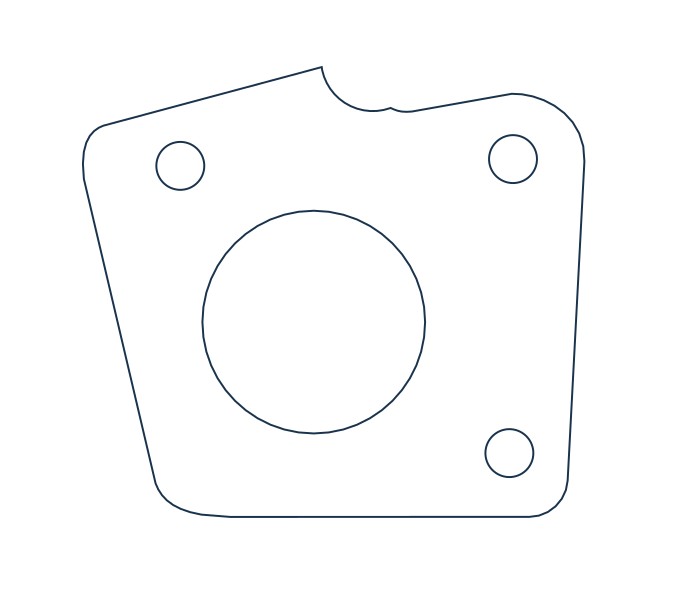
Перед дальнейшей работой над деталью, нужно убедиться что кривизна детали и все размеры сняты правильно. Для этого из обычной фотобумаги на плоттере вырезается вот такая штуковина и прикладывается в рулю. Если всё «попало», можно двигаться дальше.
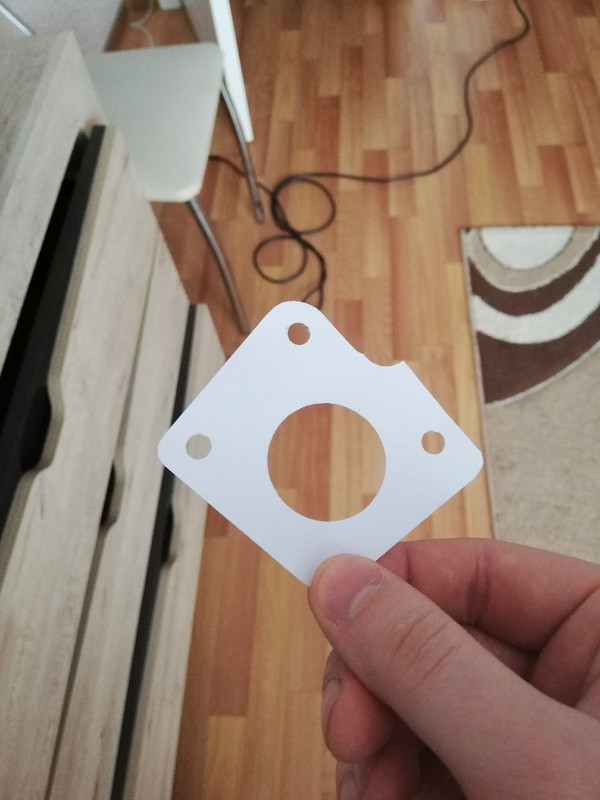
Проектирование.
Ещё на этапе зарождения идеи я был уверен, что нет ничего проще, чем снять контуры профиля, которым руль прилегает к траверсе, выточить по этому контуру деталь нужной высоты с отверстиями под болты в тех же местах и просто подставить её между рулём и траверсой, прикрутив болтами подлиннее.Столь прямолинейное решение было отвергнуто по двум причинам: 1) особенность оригинальной конструкции, заключавшаяся в декоративной пластиковой заглушке с логотипом, прикрывавшей один из трёх болтов, крепящих руль и заглушку оси рулевой колонки; 2) вероятность ухудшить обзор в зеркалах, просто подняв руль (т.к. зеркала находятся на корпусе мотоцикла, ниже уровня грипсов)
И если с потерей декоративной заглушки ради комфортной посадки иной райдер ещё может смириться (хотя я категорически не хотел), то ухудшение обзора абсолютно неприемлемо.
Так родилась идея сделать площадку, с… ещё одной площадкой под руль, смещённой относительно оригинальной нормали и немного наклонённую на райдера. Чтобы лучше представлялось, забегая вперед покажу одну из первых итераций детали.
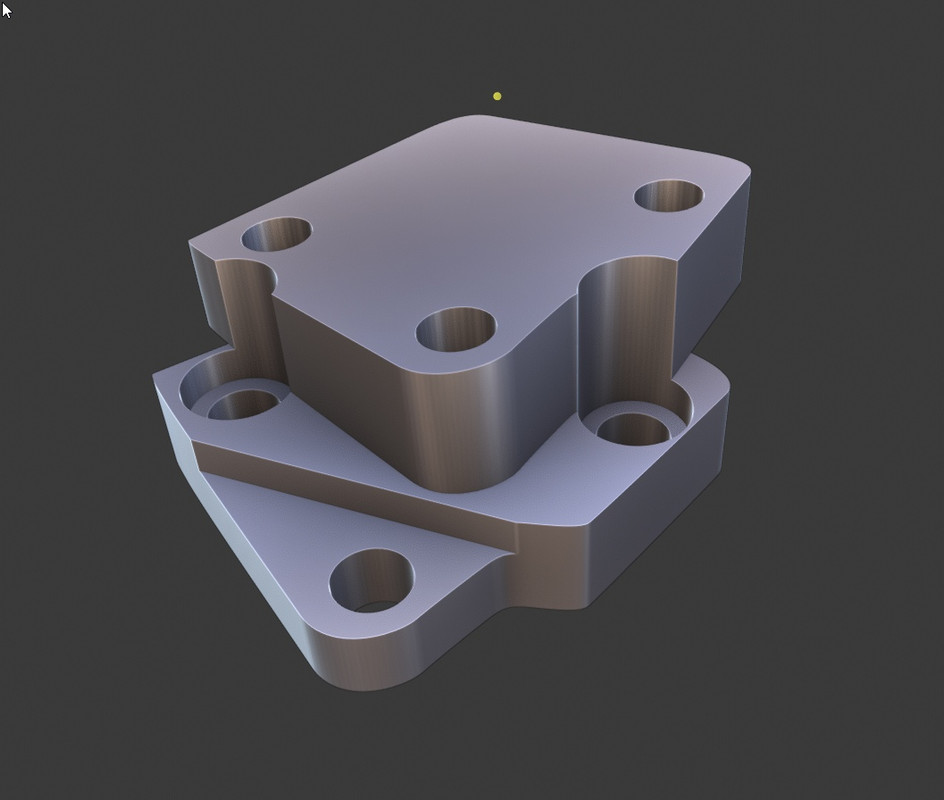
Профессия моя никак не связана с чертежной или проектировочной деятельностью, поэтому этап создания чертежа я пропустил и сразу приступил к созданию 3D модели. Благо с компьютерной графикой моя профессия связана напрямую, этот этап был самым простым и предсказуемым. Для создания модели я выбрал софт, в котором работаю каждый день — Blender 3D и аддон (плагин) Sverchok, для параметрического моделирования. Кто не знаком с нюансами, кратко поясню — параметрическое создание модели означает, что в противовес классическому «ручному» моделированию, геометрия генерируется на основе вводимых параметров и координат, в не деструктивной манере (т.е. на любом этапе создания геометрии любой параметр можно отредактировать и вся модель пересчитается заново). Такой подход позволил быстро и безболезненно вносить изменения в последующие итерации детали.
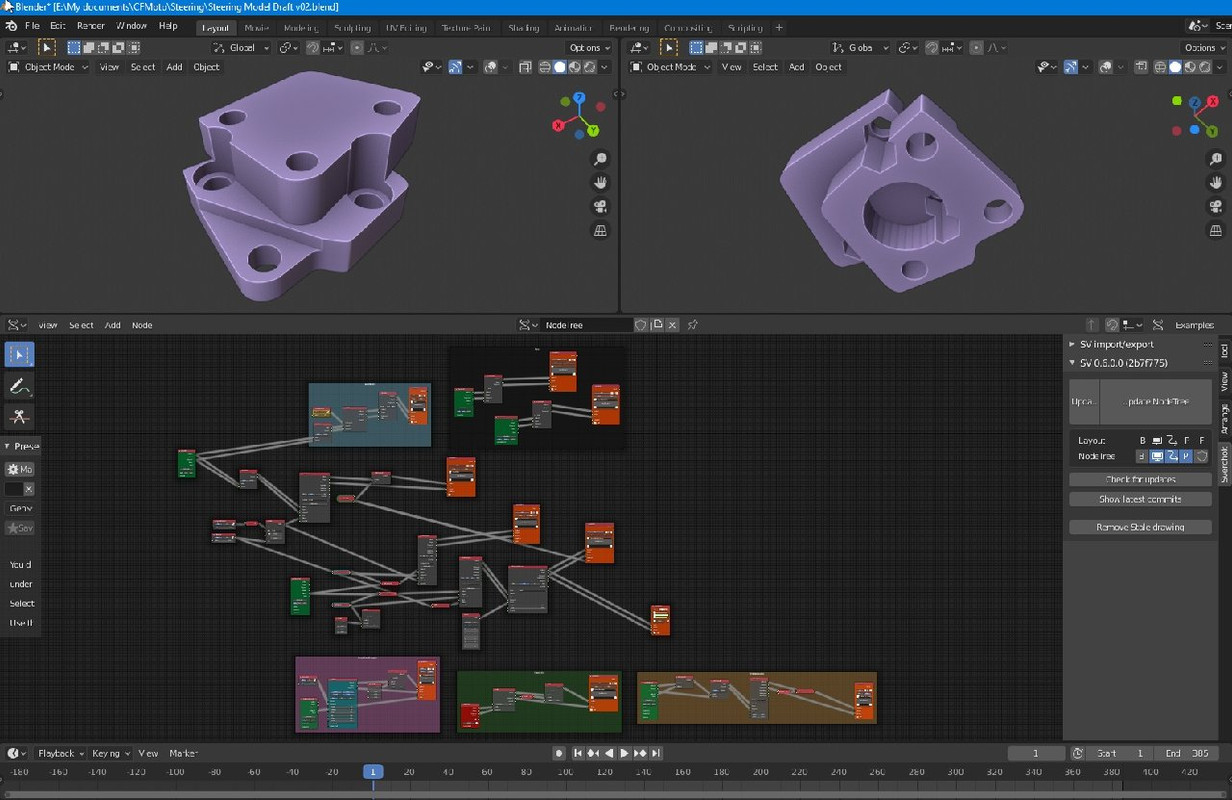
Воплощение.
Версия v03 проекта после мелких правок была готова к прототипированию на 3D принтере. Печатный прототип не должен обладать прочностными характеристиками, поэтому был выполнен из самого недорогого ABS пластика с минимальным заполнением, но максимальной точностью в размерах. Обошелся он мне в 500 рублей и, будучи установленным на руль, позволил убедиться в состоятельности концепта и внести некоторые мелкие поправки.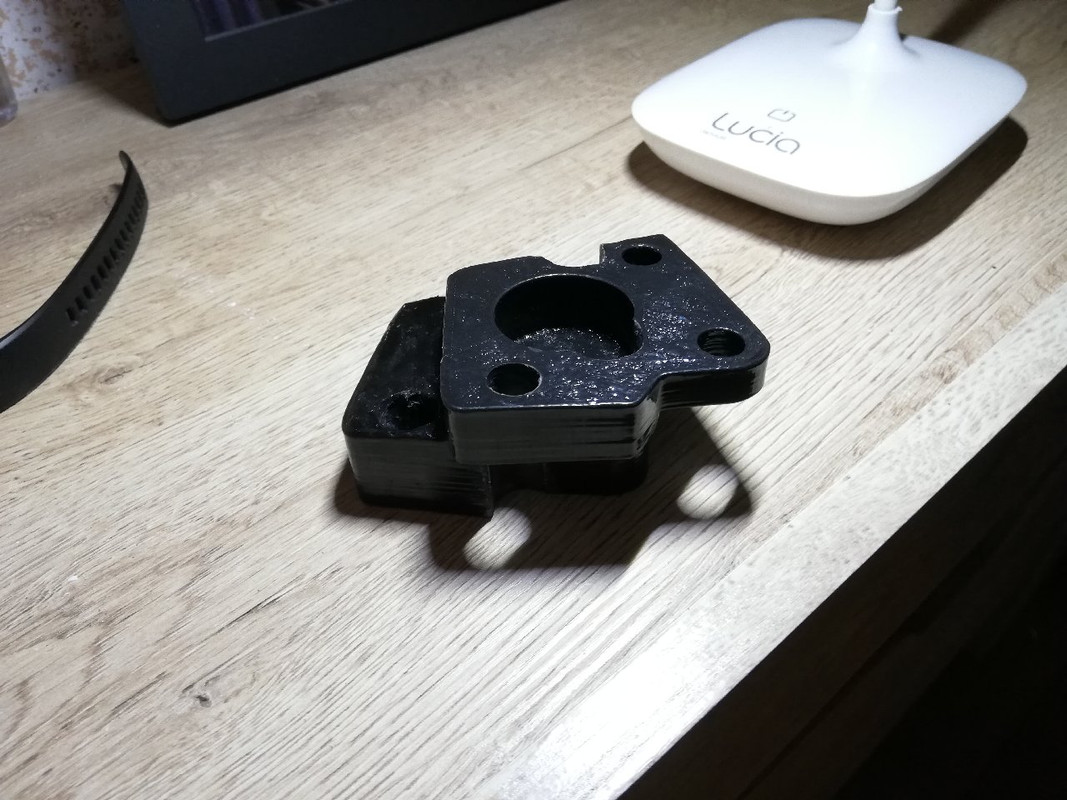
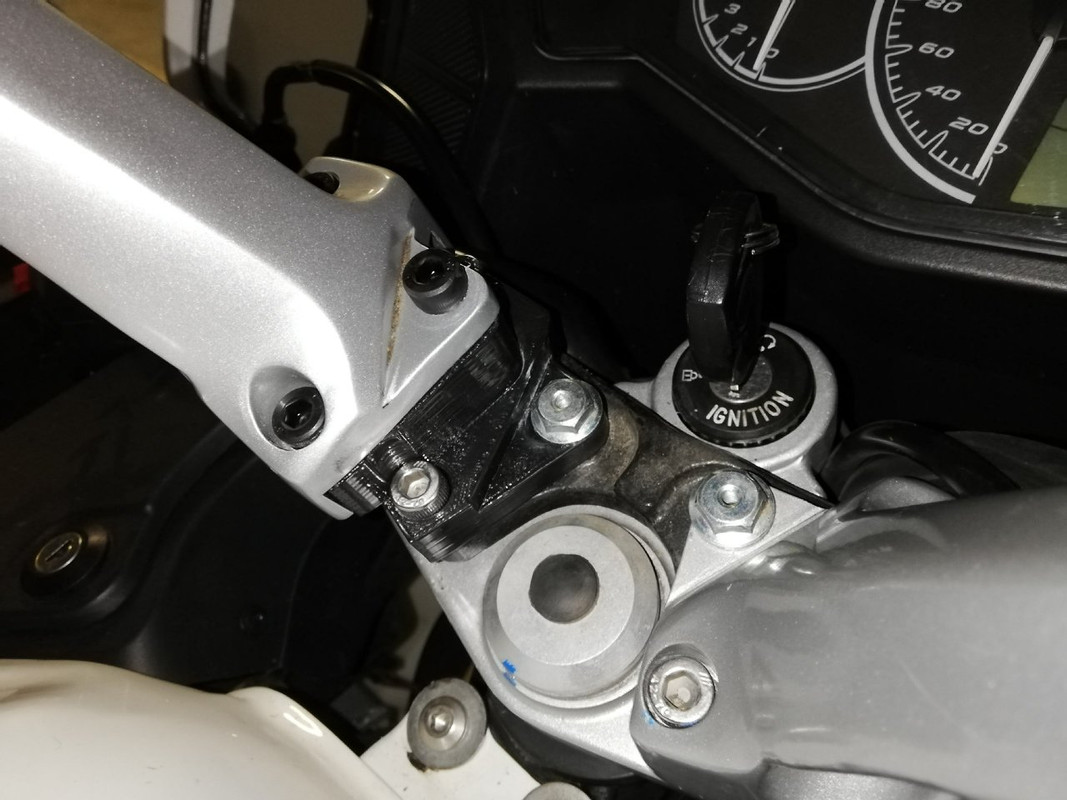
Окрылённый успехом, я незамедлительно начал поиски производства, на котором мою деталь, наконец, воплотят в благородном металле… ну, или, хотя бы в алюминии. Вот тут и дала о себе знать моя нехватка знаний в смежной области :) Первая моя ошибка заключалась в святой уверенности в том, что куда ни плюнь — попадешь во фрезерный станок с ЧПУ. Это ВНЕЗАПНО! оказалось не так. Найти станок (с грамотным мастером в придачу) в моём родном городке с населением в 50 тысяч оказалось непросто. Тут вылез мой второй промах — уверенность в том, что каждое производство хранит специально для меня алюминиевый брусок нужного размера. Это тоже оказалось не так. В общем, безрезультатно пошукав помощи через знакомых знакомых, я полез строчить объявление в интернет. Благо, живём в 21 веке и доставка всего и вся из разных уголков страны нынче дело простое и доступное. Поиски в соц-сетях привели меня в паблик ВК, этакий «черный рынок» мастеров мех.обработки, халтурящих в свободное время на производственных мощностях. Я разместил объявление о найме и стал ждать. Примерно через неделю ко мне в личку постучались сразу несколько специалистов. Я подробно обрисовал им картину, показал деталь с различных ракурсов и попросил предварительной оценки бюджета и сроков. На этом этапе меня настигло самое жестокое откровение — до сих пор я (почему-то) был уверен, что на ЧПУ станке можно сделать абсолютно любую загогулину. Но и это, черт возьми, оказалась не так! :) Запоздалое изучение вопроса показало, что станки бывают трёх-, пяти-, семи- и ещё чёрт-знает-сколько-осевые. И то, что можно выполнить на одном станке, либо невозможно, либо крайне трудозатратно на другом. Моя фантазия, не ограниченная этим знанием, родила деталь как раз обладающую свойствами «невыполнимости» на самом распространённом — трёх-осевом станке. Скрепя сердце, я принялся дорабатывать и упрощать модель. В частности, пришлось избавиться от того самого наклона руля, немного приподняв его и развернув на себя по продольной оси на 3 градуса. После всех пертурбаций в работу-таки отправилась аж восьмая версия проекта.
Но и на этом препоны не кончились! Модель, будучи изготовленной в софте не заточенном под инженерное моделирование, даже конвертированная в популярные «кадовские» обменные форматы, типа .step и .iges, не годилась для составления рабочей программы ЧПУ станка. Поэтому мне, никогда ранее не работавшему с CAD софтом, не оставалось ничего, кроме как за пару вечеров разобраться с замечательным пакетом FreeCAD и практически с нуля воссоздать деталь в ней по всем канонам и правилам. Не буду скрывать, что, учитывая полное отсутствие опыта, качеством получившейся модели я был горд.
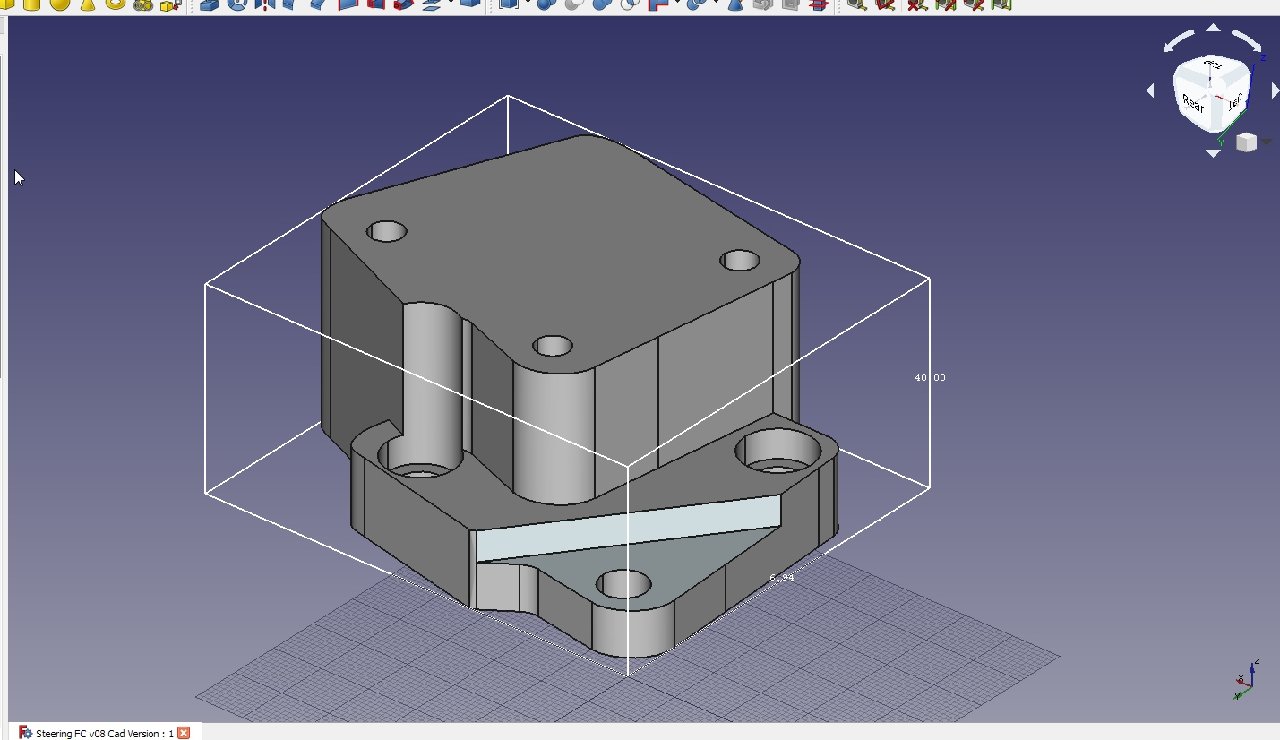
Дальнейшее общение с потенциальными исполнителями лишний раз напомнило мне о том, что такое «бизнес по-русски». Один предложил мне выточить обе детали за 10 тысяч рублей, при этом работая на ручном фрезерном станке в течении пары тройки недель :) Я не знаю, насколько он крутой мастер, но для меня так и осталось загадкой, как он собирался вручную выточить две абсолютно симметричные детали. Другой взялся за работу без лишних вопросов, за божеские 4 тысячи рублей и в недельный срок. Точил точил целый месяц, периодически извиняясь за задержки. Через месяц сообщил что обе детали, наконец, готовы и… после просьбы прислать фотографию с контрольными замерами просто перестал отвечать на сообщения :) К чему был весь этот спектакль, я так и не понял, учитывая, что я даже не делал никаких предоплат. Наконец, я всё-таки нашёл, казалось бы адекватного исполнителя по адекватной цене, да ещё и относительно недалеко от меня. Человек рассмотрел модель, уточнил некоторые нюансы, озвучил бюджет в 5 тысяч рублей и приступил к работе. Но, через полторы недели ВНЕЗАПНО! выяснилось, что изготовление требует дополнительных трудозатрат и надо бы накинуть пару тыщенок (предоплат я, опять же, не делал). Я сказал, что пару дней подумаю, но сам был настроен категорически против такого подхода. Я сам оказываю людям профессиональные услуги и в моей практике бывают сложные заказы, в процессе работы над которыми возникают неучтенные мной нюансы. Но если я перед началом работ озвучил клиенту цену, я никогда не приду к нему с просьбой добавить денег, потому что я хреново посчитал. В общем, услышав от меня отказ, мастер выполнил работу по первоначальной цене, т.к. в противном случае он просто остался бы с двумя ненужными деталями, а я бы не поленился найти другого исполнителя :)
Неделю спустя я забрал многострадальные детальки из офиса службы доставки. Вращая в руках два увесистых блестящих кусочка алюминия я дивился тому, как моя инженерная мысль сначала обрела форму на экране монитора, а затем и в реальном твёрдом металле. Чрезвычайно приятное чувство :)
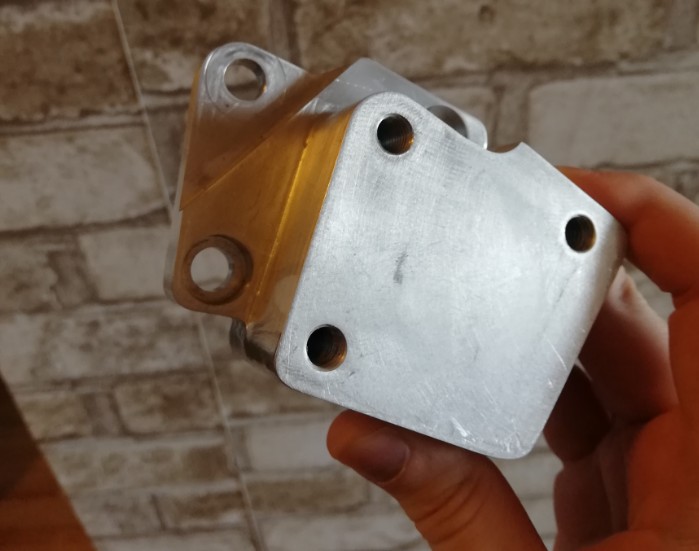
Оставалось только покрыть детали бесцветным акриловым лаком (для защиты от коррозии) и установить, наконец, на мотоцикл. Сама по себе установка заняла минут десять. В процессе я обнаружил неучтенный момент — длину электрической косы, идущей к пультам. В общем, будь проставки ещё чуть выше и все усилия вполне могли бы оказаться напрасными, т.к. встало это всё в натяг :)
В итоге.
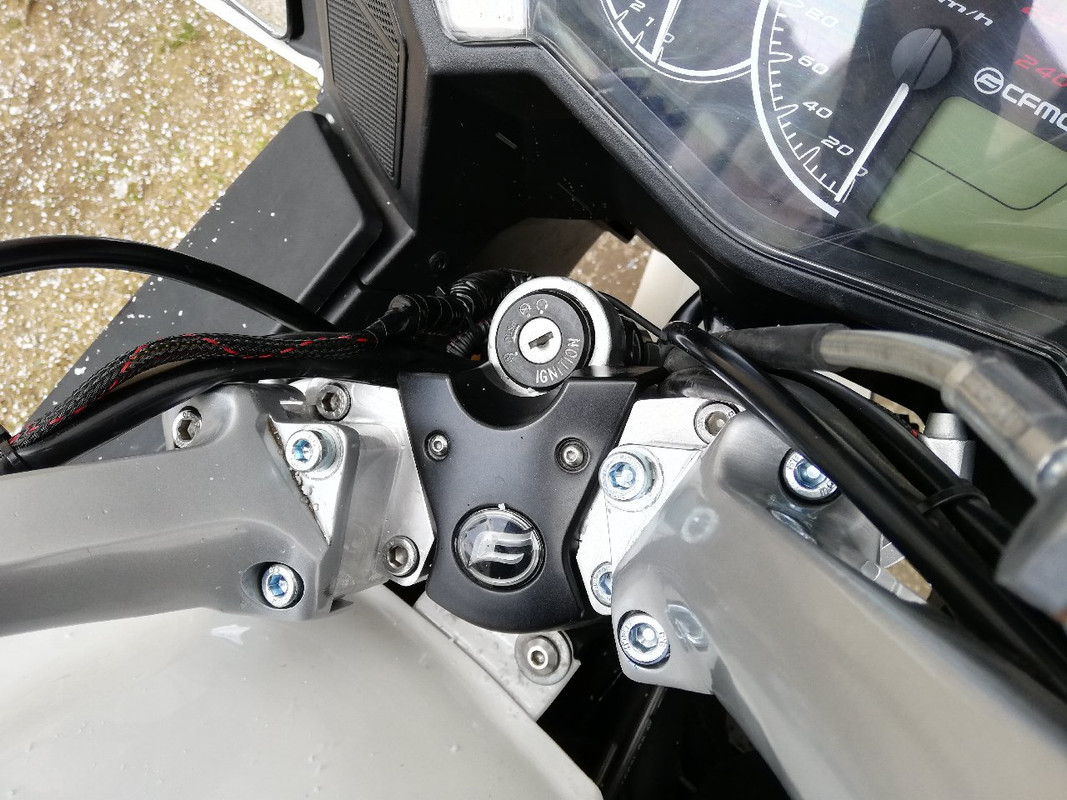
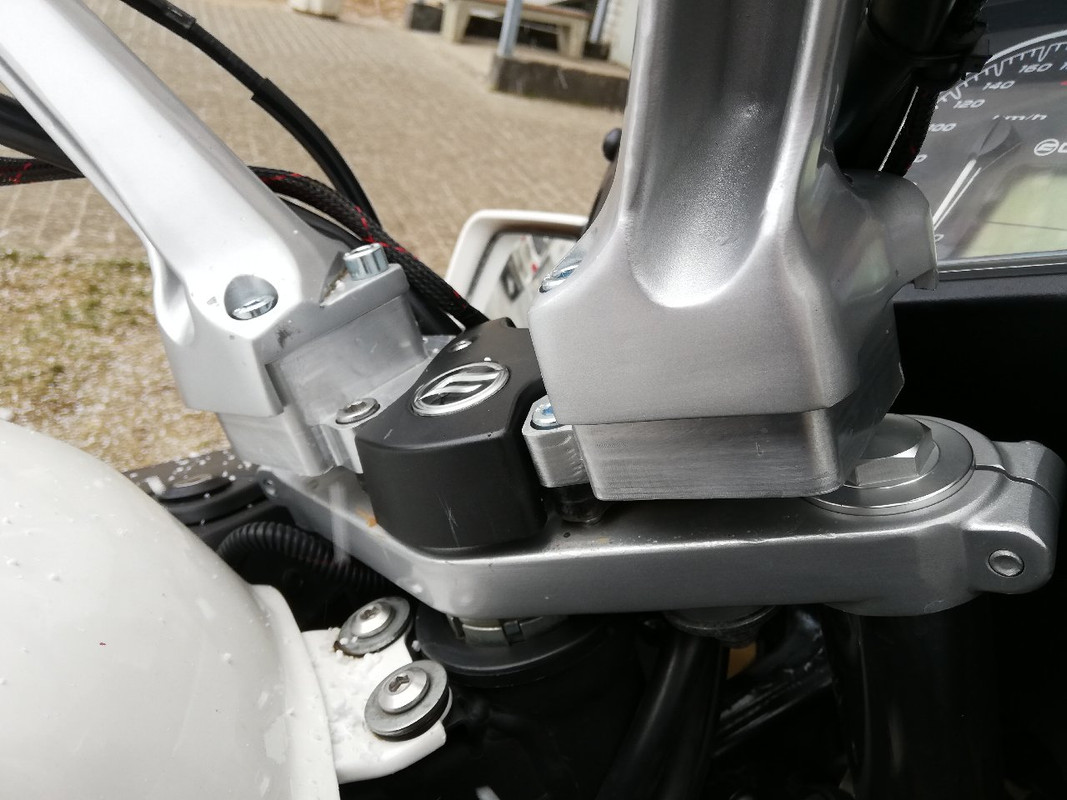
Руль стал на 37 мм выше, самую малость шире и немного развернут ко мне. Искомый эффект достигнут — посадка теперь более расслаблена, руки согнуты в локтях, запястья просто лежат на руле. Обзор в зеркала на удивление даже стал чуть лучше. Из ожидаемых минусов только изменившиеся ощущения от активной рулежки на малых скоростях, но это как раз то, чем я могу пожертвовать ради комфорта в дальней дороге.
Весь проект занял около трёх месяцев (два из которых мне вытачивали деталь) и обошелся мне примерно в 6 тысяч рублей, что, учитывая цены на подобный тюнинг для других известных мотоциклов, по-моему совсем не дорого. И, конечно, сложно переоценить количество полученного опыта и новых знаний в смежных областях.
Надеюсь, чтиво было интересным, а кому-нибудь и полезным. Спасибо, что дочитали до конца! С открытием сезона и здоровья всем! :)
Sergusster
- Сергей Метельский
- 1 апреля 2020 в 2:43
- 5
- ?

- AndrewGorgaR
- 1 апреля 2020 в 4:21
- ↓
А какой прогой пользовался для фотограмметрии? Иногда прям очень надо для решения похожих задач.

За день? Сложно представить даже имея стандартный инструмент в гараже, который скорее всего ничем не поможет для изготовления таких проставок. Поделитесь мыслями, как изготовить такое самому за день без спец. инструмента и материала? Раз уж вы так легко и искромётно опускаете пост, в котором человек поделился своим опытом.

Можно изготовить за один день.
НО для этого надо иметь заинтересованного, мотивированного фрезеровщика с необходимым оборудованием, инструментом и материалом, при этом сделать с первого раза, получив результат вас удовлетворяющий, в общем — конь в вакууме, сферический.
Автор провёл хорошую конструкторскую работу, потом технологическую доработку, получил модель с изменяемыми и контролируемыми параметрами, с возможностью многократного повторения и модификации, по сути получил деталь для серийного изготовления. Остаётся вопрос, а надо было так делать ради одного комплекта?
НО для этого надо иметь заинтересованного, мотивированного фрезеровщика с необходимым оборудованием, инструментом и материалом, при этом сделать с первого раза, получив результат вас удовлетворяющий, в общем — конь в вакууме, сферический.
Автор провёл хорошую конструкторскую работу, потом технологическую доработку, получил модель с изменяемыми и контролируемыми параметрами, с возможностью многократного повторения и модификации, по сути получил деталь для серийного изготовления. Остаётся вопрос, а надо было так делать ради одного комплекта?

- Sergusster
- 1 апреля 2020 в 11:49
- ↑
- ↓
Ну, ради одного комплекта или двадцати — вариантов у меня особо не было, минимальный объем работ останется неизменным :) Сам процесс конструирования, несмотря на обилие текста занявший всего несколько свободных вечеров, мне не доставил никаких хлопот. Напротив, был увлекательным и принёс ценный опыт разработки. Так что, сплошной профит :) Теперь подумываю о конструировании и изготовлении занижаек подножек

- Sergusster
- 1 апреля 2020 в 10:21
- ↑
- ↓
Сдается мне, вы диванный аналитик, сэр. Ибо даже не считая времени изготовления модели и рабочей программы (а это уже несколько часов минимум), чистое машинное время работы ЧПУ станка на ОДНУ деталь составило 102 минуты :))

- capitan_amer
- 1 апреля 2020 в 7:56
- ↓
всё в ручную можно было сделать, тем более из люминьки
плохо что нет фоток сбоку мотоцикла, было, стало
плохо что нет фоток сбоку мотоцикла, было, стало

все делается вручную и быстрее поисков мастера. Сам делал проставку для левой подножки. Форма конечно немного проще — 3 отверстия и в середине треугольник выпилить нужно. Жалко было тратить 5 косарей за кусок алюминия. тоже сначала сделал 3д модель за пару часов максимум, на принтере напечатал. Правда хватало от 1000км до 3х. Потом решил воплотить в металле — эти сраные ЧПУ-шники просили от 5 за деталь. В итоге кусок плиты Д16Т за 400руб, болгарка (была), пара перьевых сверел (купил за 200р оба) и дремель (был) решили проблему.

- EiskiyKolhoznik
- 1 апреля 2020 в 8:36
- ↓
Хотел пластиковые заглушки как-то сделать по образу оригинальных с помощью фотограмметрии. Даже отфоткал, но затем, посчитав сколько в дальнейшем придется это дело доводить, плюнул и заказал за бешеные деньги для 100 грамм пластика из Японии.
На словах легко, а на деле слишком много возни.
На словах легко, а на деле слишком много возни.

При наличии рук изготовить самому не проблема, вручную делал и посложнее, проги и 3д не имею, только руки, мозг, инструмент и гараж. Иногда дольше ищешь материал и долго примеряешься, ну и вдохновение иногда нужно, пинок, что бы в голове не было семейных и других проблем а только поставленная задача. Ножовка, болгарка, наждак, тиски, набор напильников, набор наждачки и уединение в гараже. Спасибо за статью, вдохновит неуверенных.

- Sergusster
- 1 апреля 2020 в 10:35
- ↑
- ↓
Я сразу оценил вероятность нахождения такого рукастого мастера близкой к нулю. Ну и, будем честны — ручная работа такой сложности в любом случае будет стоить дороже работы ЧПУ станка. Собственно… удешевление и есть суть существования различных станков и конвейеров :) Ну и, немаловажный аспект — отдавая модель в ЧПУ обработку я знаю, что с 99% вероятностью получу то, что видел у себя на экране.

Удешевление в контексте маломальски серийного производства — безусловно.
Единичную деталь все же бывает проще выполнить вручную. Особенно, если подзабить на эстетику и производственную культуру(читай, приварить руль один раз и навсегда на удобном месте под удобным углом после нескольких прикидок). Не предлагаю — констатирую =) Цена вопроса бывает дешевле на пару порядков, и времени тоже. Но смотреть на это не так приятно, да.
Единичную деталь все же бывает проще выполнить вручную. Особенно, если подзабить на эстетику и производственную культуру(читай, приварить руль один раз и навсегда на удобном месте под удобным углом после нескольких прикидок). Не предлагаю — констатирую =) Цена вопроса бывает дешевле на пару порядков, и времени тоже. Но смотреть на это не так приятно, да.

- DFrost2007
- 1 апреля 2020 в 12:53
- ↓
Молодец! Хорошую работу проделал. Теперь каждый раз будешь садиться на мот и думать, какой ты рукастый умничка))) Если бы выточил где-то на заказ, то такого эффекта бы не было))

«Вручную»...«можно было бы»...«за день»… В этой цепочке не хватает пары фраз про «знакомого сварщика, кто сварил бы из… и палок за пять минут». Человек сделал сам, причем с замера и моделирования прошел через прототипирование до конечного результата. Да еще и спалил в широкий доступ пару инструментов. Это не чета добыче жирного каталога и семафорным пляскам с банковской картой. Аля «куплю кастом на заводе»)))) Грамотный подход, качественный результат. За такое уже респект. Цена и сроки в данном случае дело десятое.

- Sergusster
- 2 апреля 2020 в 12:39
- ↑
- ↓
Опыта с фрикадом у меня не шибко много (хотя после проставок я делал в нём ещё несколько моделей для других проектов), но вообще софтина приятно удивила. Выглядит и чувствуется как вполне себе коммерческий, конкуренто-способный софт с приличным функционалом. Но, повторюсь, мне не с чем сравнить. Никаких вылетов и ошибок не было, всё стабильно. FreeCAD получил на моём компе постоянную прописку :)

- Sergusster
- 2 апреля 2020 в 12:35
- ↑
- ↓
Литьё в мелкосерийном производстве это ещё менее целесообразно, чем ЧПУ обработка. Очень хлопотно. Даже если представить что с 3D печати получилась идеальная модель (а такого не бывает, если это не фотополимерный принтер), то выжечь из формы обычный пластик проблематично, надо печатать «воском». Затем надо грамотно лить металл под давлением, потом срезать литники, механически обрабатывать получившуюся деталь… в общем, ерунда :)) С ЧПУ станка практически за пару часов выходит чистовое изделие

- Lawrence_Fox
- 3 апреля 2023 в 12:34
- ↓
Пролюбил я этот пост, работа проделана великолепная. Тоже хочу руль поднять, кисти забиваются. Почем деталька такая, если не секрет?
Только зарегистрированные пользователи могут оставлять комментарии.
Войдите, пожалуйста, или зарегистрируйтесь.
Комментарии (35)
RSS свернуть / развернуть