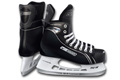
- Пробег для публикации поста в сообщество: 50.00 км
- Читателей: 2693 | Постов: 2109
Обозреваем, тестируем нашу вторую кожу=) А также новинки и тому подобные радости)
Администраторы (1)
Модераторы (0)
Модераторов здесь не замеченоЧитатели (2686)
Bodya Mila none10 Integra Flash HAYABUSA Osama TriAl Urlak Malashka KOSHKA Stich glyaks100 Denis aLexusPro ArSoron Core spamer80 Konditer Maxi nbaksalyar smile ginecolog Oziris DiYamaha RedLine RMZS insideR Jay MeCrazyJunkie Turners Satt 3dinfo Wishka Bike-TV SirNik Vacelica Magnus Alan Shkiper Hydrophonic teroff shakawkaw Boatik pmg Dragem Marcus egoisto olegrem SerchВсе читатели
Экипировка → Экскурсия на производственную фабрику Sidi
В Мазере, находящейся менее чем в 100 км от Венеции, расположено новое здание фабрики компании Sidi, которая открывает перед нами свои двери. Мы проходим просторный холл, где расставлены мотоботы, защищавшие ноги многих знаменитостей мотоспорта, и направляемся в шоу-рум, где представлены все модели марки: от трековых до туринговых, от внедорожных до супермото. Обувь расставлена настолько ровно, что возникает ассоциация с солдатами на параде.
Но то, что интересует нас, находится на нижних этажах – там, где расположены сборочные линии – автоматизированные, и в то же время с большой долей участия людей.
>
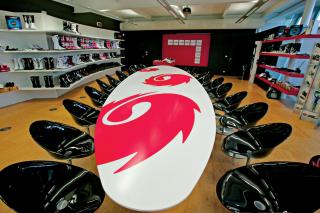
ИЗ ИТАЛИИ В РУМЫНИЮ… И ОБРАТНО В ИТАЛИЮ
Несмотря на то, что окончательная сборка и проверка качества продукции Sidi происходит в Италии, кройка и сборка некоторых частей ботинка производится далеко от Аппенинского полуострова. Все начинается здесь, в провинции Тревизо, первый шаг — прием и проверка всего сырья (вне зависимости от модели). На верхних этажах фабрики стоят большие коробки, заполненные стельками, рулонами искусственной кожи Lorica (произведенной в Италии) или Mesh из Германии, которые ждут отправки: материалы для изготовления нижних моделей линейки – в Румынию, а топовых – на грузовом лифте на нижний этаж, где расположен цех.

Но как узнать, где была произведена обувь? Очень просто: топовые модели производятся в Италии, нижние – в Румынии, а промежуточная линейка – в обеих странах…
Желтые лекала для велообуви, зеленые для мото: для того чтобы избежать путаницы к каждой колодке разного размера вручную крепится соответствующая стелька. Так начинается первый этап долгого процесса производства мотообуви…
На итальянском заводе работают в общей сложности 80 человек, а в Румынии около 250, которые занимаются сборкой 400-500 деталей для моделей Crossfire или Vortice примерно за 4-5 часов.


За «пиковый» период, с января по июнь, за день удается собрать около 2500 пар обуви. Конечно же, производство автоматизировано, но все же множество людей участвуют в этом процессе. Ключевое слово: качество. А для того, чтобы получить качественный конечный результат, на многих этапах требуется участие человека…


СШИТЫ И СКЛЕЕНЫ ВРУЧНУЮ
Следующий этап начинается, когда все части «паззла», выкроенные из искусственной кожи Lorica, уже сшиты и начинают приобретать форму сапога. В заготовку устанавливают жесткий задник и носок из термоформованного полиуретана. Затем устанавливаются застежки. Этот процесс продолжается до тех пор, пока не получится сапог, в котором не хватает только подошвы и нескольких мелких деталей.
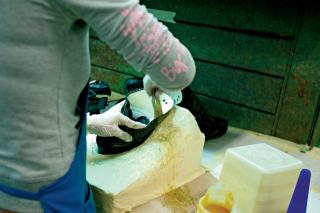
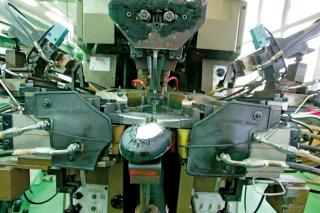
Подкладку из водонепроницаемого материала Gore-Tex, использующуюся для моделей высшей ценовой категории, вшивают так же вручную, поскольку некачественные соединения могут стать причиной нежелательного попадания воды вовнутрь сапога.
Дальше сапог приобретает свою окончательную форму. Сначала он попадает в машину, которая нагревает переднюю часть с уже установленным носком, чтобы придать ей закругленную форму. Одновременно автомат загибает края заготовки к подошве и крепит их скобами к колодке вместе с подошвой. Сочетание давления, температуры (50-60° C) и времени воздействия придает будущему сапогу привычную для каждого форму. Этот процесс называется затяжка.
Обувь, произведенная на фабрике Sidi, очень удобна, в том числе и благодаря приклеенной подошве – принцип, по которому производят 90% продукции. Этот непростой процесс происходит в мастерской по установке подошвы.
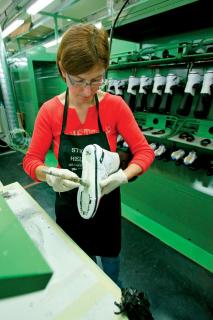

После снятия вспомогательных скоб со стельки происходит первая проклейка, чтобы соединить стельку с краем искусственной кожи Lorica. На этом этапе сапог попадает под пресс, и очень важно удержать все детали на месте. Затем происходит этап шлифовки, на котором удаляют все, что может помешать подошве хорошо приклеится и причинять неудобство мотоциклистам.
МНОГОЭТАПНАЯ ПРОКЛЕЙКА
Для производителя важнее всего качество продукции, поэтому скоростью производства управляет не машина, а человек.
В положении «вверх подошвами» мотоботы Sidi сохнут и ждут своей очереди, чтобы попасть в руки другого мастера и обзавестись соответствующей подошвой. Установка системы SRS (Sole Replacement System – «Система замены подошвы», которая позволяет заменить сношенную подошву) на мотобот Crossfire – непростой этап.

Чтоб избежать ошибок, место, куда должна быть приклеена подошва, отмечают черным скотчем. Первая смазка клеем сапога и подошвы, обсушка, второе нанесение клея, но на этот раз уже черного цвета, снова обсушка. Теперь можно снять скотч.
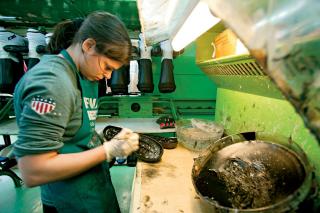
Чтобы подошва приклеилась как следует, сапоги и подошвы разогревают в особой печи, а затем направляют под пресс. После отведенного времени под прессом, когда подметка окончательно приклеивается, из сапога извлекают колодку. Теперь мотобот практически готов, остается только установить внешние элементы защиты и застежки. Все это делается вручную. Последний этап — контроль качества. Проверяется каждый сапог!

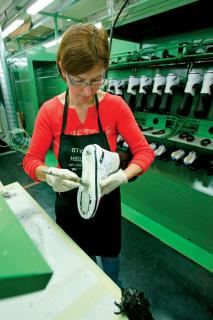
УПАКОВКА
Во время последней проверки перед упаковкой просматривают все швы и места склейки мотоботов Sidi, чтобы гарантировать качество готового продукта. В случае обнаружения недостатков еще есть возможность их исправить. Все в порядке, и мотоботы отправляются в коробку ждать отправки в страну назначения.
Многие внешние детали сменные, их довольно легко можно заменить на новые, что позволяет продлить срок эксплуатации ботинок.
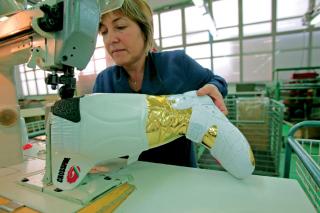
ИССЛЕДОВАТЕЛЬСКИЙ ЦЕНТР
Всего 2 человека занимаются исследованием и проектированием новой продукции: развитие, новые технология, смена цветов – все важные изменения происходят здесь – в правом крыле здания, где расположено конструкторское бюро. Затем их утверждают основатель марки Sidi Дино Синьори и его команда.
Но то, что интересует нас, находится на нижних этажах – там, где расположены сборочные линии – автоматизированные, и в то же время с большой долей участия людей.


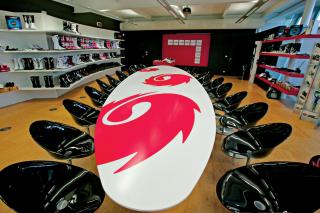

ИЗ ИТАЛИИ В РУМЫНИЮ… И ОБРАТНО В ИТАЛИЮ
Несмотря на то, что окончательная сборка и проверка качества продукции Sidi происходит в Италии, кройка и сборка некоторых частей ботинка производится далеко от Аппенинского полуострова. Все начинается здесь, в провинции Тревизо, первый шаг — прием и проверка всего сырья (вне зависимости от модели). На верхних этажах фабрики стоят большие коробки, заполненные стельками, рулонами искусственной кожи Lorica (произведенной в Италии) или Mesh из Германии, которые ждут отправки: материалы для изготовления нижних моделей линейки – в Румынию, а топовых – на грузовом лифте на нижний этаж, где расположен цех.

Но как узнать, где была произведена обувь? Очень просто: топовые модели производятся в Италии, нижние – в Румынии, а промежуточная линейка – в обеих странах…
Желтые лекала для велообуви, зеленые для мото: для того чтобы избежать путаницы к каждой колодке разного размера вручную крепится соответствующая стелька. Так начинается первый этап долгого процесса производства мотообуви…
На итальянском заводе работают в общей сложности 80 человек, а в Румынии около 250, которые занимаются сборкой 400-500 деталей для моделей Crossfire или Vortice примерно за 4-5 часов.


За «пиковый» период, с января по июнь, за день удается собрать около 2500 пар обуви. Конечно же, производство автоматизировано, но все же множество людей участвуют в этом процессе. Ключевое слово: качество. А для того, чтобы получить качественный конечный результат, на многих этапах требуется участие человека…


СШИТЫ И СКЛЕЕНЫ ВРУЧНУЮ
Следующий этап начинается, когда все части «паззла», выкроенные из искусственной кожи Lorica, уже сшиты и начинают приобретать форму сапога. В заготовку устанавливают жесткий задник и носок из термоформованного полиуретана. Затем устанавливаются застежки. Этот процесс продолжается до тех пор, пока не получится сапог, в котором не хватает только подошвы и нескольких мелких деталей.
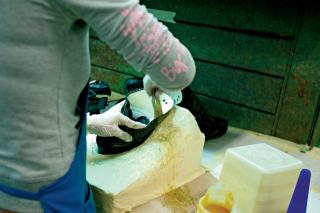
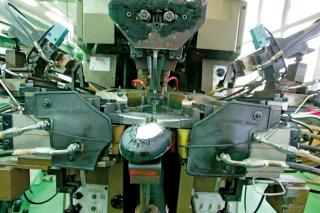
Подкладку из водонепроницаемого материала Gore-Tex, использующуюся для моделей высшей ценовой категории, вшивают так же вручную, поскольку некачественные соединения могут стать причиной нежелательного попадания воды вовнутрь сапога.
Дальше сапог приобретает свою окончательную форму. Сначала он попадает в машину, которая нагревает переднюю часть с уже установленным носком, чтобы придать ей закругленную форму. Одновременно автомат загибает края заготовки к подошве и крепит их скобами к колодке вместе с подошвой. Сочетание давления, температуры (50-60° C) и времени воздействия придает будущему сапогу привычную для каждого форму. Этот процесс называется затяжка.
Обувь, произведенная на фабрике Sidi, очень удобна, в том числе и благодаря приклеенной подошве – принцип, по которому производят 90% продукции. Этот непростой процесс происходит в мастерской по установке подошвы.
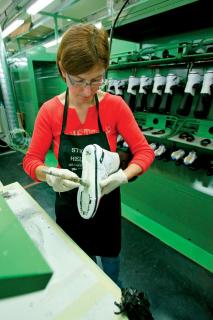

После снятия вспомогательных скоб со стельки происходит первая проклейка, чтобы соединить стельку с краем искусственной кожи Lorica. На этом этапе сапог попадает под пресс, и очень важно удержать все детали на месте. Затем происходит этап шлифовки, на котором удаляют все, что может помешать подошве хорошо приклеится и причинять неудобство мотоциклистам.
МНОГОЭТАПНАЯ ПРОКЛЕЙКА
Для производителя важнее всего качество продукции, поэтому скоростью производства управляет не машина, а человек.
В положении «вверх подошвами» мотоботы Sidi сохнут и ждут своей очереди, чтобы попасть в руки другого мастера и обзавестись соответствующей подошвой. Установка системы SRS (Sole Replacement System – «Система замены подошвы», которая позволяет заменить сношенную подошву) на мотобот Crossfire – непростой этап.

Чтоб избежать ошибок, место, куда должна быть приклеена подошва, отмечают черным скотчем. Первая смазка клеем сапога и подошвы, обсушка, второе нанесение клея, но на этот раз уже черного цвета, снова обсушка. Теперь можно снять скотч.
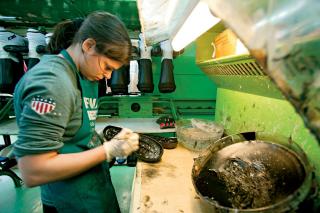
Чтобы подошва приклеилась как следует, сапоги и подошвы разогревают в особой печи, а затем направляют под пресс. После отведенного времени под прессом, когда подметка окончательно приклеивается, из сапога извлекают колодку. Теперь мотобот практически готов, остается только установить внешние элементы защиты и застежки. Все это делается вручную. Последний этап — контроль качества. Проверяется каждый сапог!

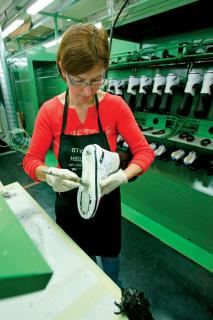
УПАКОВКА
Во время последней проверки перед упаковкой просматривают все швы и места склейки мотоботов Sidi, чтобы гарантировать качество готового продукта. В случае обнаружения недостатков еще есть возможность их исправить. Все в порядке, и мотоботы отправляются в коробку ждать отправки в страну назначения.
Многие внешние детали сменные, их довольно легко можно заменить на новые, что позволяет продлить срок эксплуатации ботинок.
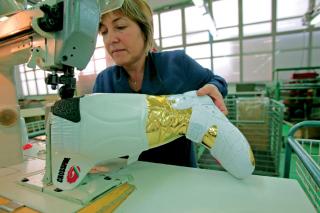
ИССЛЕДОВАТЕЛЬСКИЙ ЦЕНТР
Всего 2 человека занимаются исследованием и проектированием новой продукции: развитие, новые технология, смена цветов – все важные изменения происходят здесь – в правом крыле здания, где расположено конструкторское бюро. Затем их утверждают основатель марки Sidi Дино Синьори и его команда.

rita_eremina
- Рита
- 22 октября 2012 в 15:22
- 4
- +42

- Pavel_sivkov
- 23 октября 2012 в 0:18
- ↓
это только для показухи и налоговых инспекторов, на самом деле там работают дети нелегалы из индии по 18 часов в сутки.
здесь был ататат
Только зарегистрированные пользователи могут оставлять комментарии.
Войдите, пожалуйста, или зарегистрируйтесь.
Комментарии (14)
RSS свернуть / развернуть