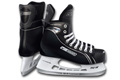
- Пробег для публикации поста в сообщество: 50.00 км
- Читателей: 2693 | Постов: 2109
Обозреваем, тестируем нашу вторую кожу=) А также новинки и тому подобные радости)
Администраторы (1)
Модераторы (0)
Модераторов здесь не замеченоЧитатели (2686)
Bodya Mila none10 Integra Flash HAYABUSA Osama TriAl Urlak Malashka KOSHKA Stich glyaks100 Denis aLexusPro ArSoron Core spamer80 Konditer Maxi nbaksalyar smile ginecolog Oziris DiYamaha RedLine RMZS insideR Jay MeCrazyJunkie Turners Satt 3dinfo Wishka Bike-TV SirNik Vacelica Magnus Alan Shkiper Hydrophonic teroff shakawkaw Boatik pmg Dragem Marcus egoisto olegrem SerchВсе читатели
Экипировка → Путешествие по заводу Nolan Group в фотографиях
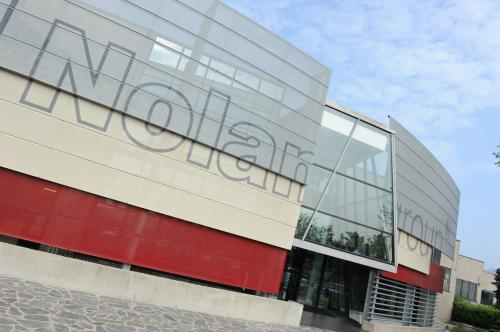
Представители компании поясняют, что подобная организация бизнеса позволяет компании контролировать производственный процесс, качество и сроки изготовления продукции, а также предоставляет возможность в случае необходимости оперативно совершенствовать продукцию. Поэтому, когда Nolan Group указывают на своих шлемах “Made in Italy”, они Вас не обманывают.
Этап 1: Изготовление подшлемников из пенополистирола
Путешествие по заводу Nolan, расположенному в итальянской коммуне Брембате-ди-Сопра, начинается с линии производства подшлемников из пенополистирола. Этот материал был выбран в качестве особого защитного слоя для современных мотошлемов по нескольким причинам. Наиболее существенные из них: доступная цена, легкий вес и надежная защита. Как ни странно, но материал, позволяющий охлаждать пиво, может быть и превосходным защитным материалом для головы. Конечно же, пенополистирол, применяемый для изготовления шлемов, отличается от белого пенообразного материала, охлаждающего упаковки с пивом, но в основном, принцип действия один и тот же.
Этот материал поставляется на фабрику в больших контейнерах, наполненных мелкими цилиндрическими гранулами. Затем эти гранулы «раздуваются» и превращаются в тот самый привычный для нас полистирол. После чего специалисты фабрики приступают к процессу формирования подшлемника.
Знаете, в чем различие между качественными и бюджетными менее эффективными моделями? Полистироловые подшлемники качественных шлемов специально разрабатываются и изготавливаются под разные размеры головы. Поэтому Nolan не признает универсальность и разрабатывает специальные подшлемники с различной плотностью, толщиной и формой в зависимости от типа и размера шлема. Т.е. для каждого пенополистиролового подшлемника проектируется отдельная форма с помощью программы CAD (системы автоматизированного проектирования), после чего она изготавливается с помощью CAM (автоматизированной системы управления технологическими процессами) на станках с компьютерным управлением. Кстати, до процесса формовки «надутый» пенополистирол по инструкции хранится в помещениях с климат-контролем.
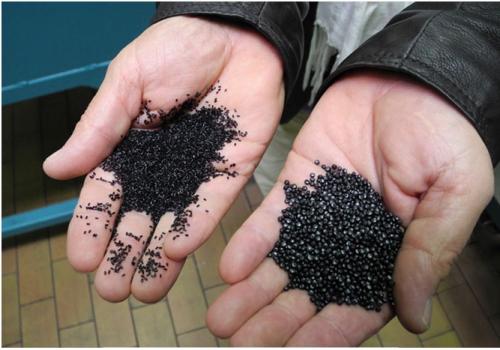
Ниже фотография формы для изготовления подшлемника. Обратите внимание на большое количество отверстий для тепла, давления и воды. Каждая из таких форм изготавливается под конкретную модель шлема.
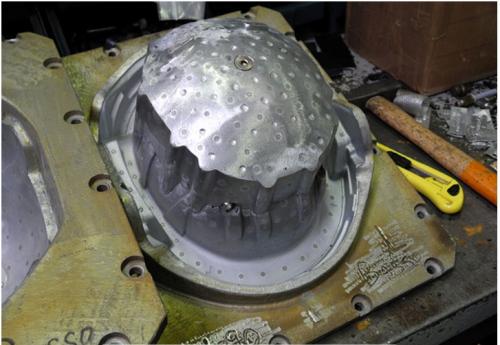
Ниже Вы видите пять формовочных станков для изготовления подшлемников. Пенополистирол подается на станки под давлением и формуется при помощи пресса. А для охлаждения формы и подшлемника используют воду
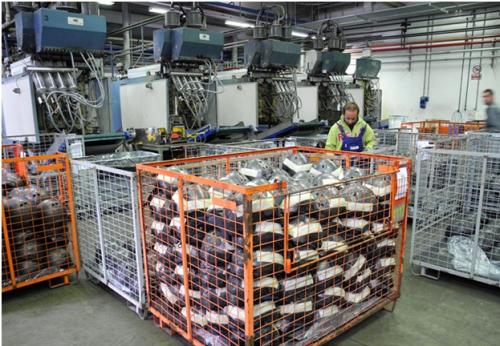
На фото изображен подшлемник из пенополистирола трех различных плотностей. Он расположен в разных частях подшлемника для того чтобы контролировать силу удара
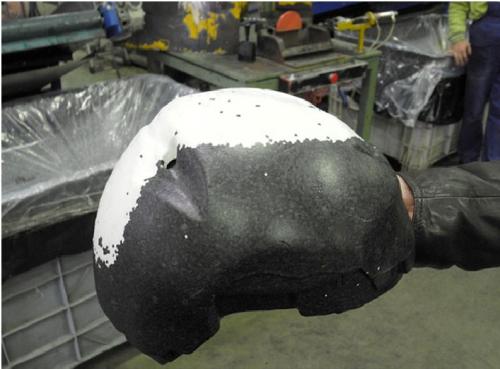
ЭТАП II: Изготовление поликарбонатной скорлупы шлема
Скорлупа шлемов Nolan Group изготавливается из поликарбоната (Nolan, Grex) и композитных материалов (X-lite). Шлем с поликарбонатной скорлупой гораздо тяжелее композитного, однако поликарбонат выдерживает весьма серьезные удары, в то время как композитная скорлупа при ударе обычно разбивается. Помните, что повторно использовать поврежденный шлем не рекомендуется. Процесс производства поликарбонатной скорлупы в корне отличается от изготовления композитной, но их объединяет то, что для обоих процессов требуются знания технологий производства и значительные затраты.
В 1972 году Nolan первыми стали производить поликарбонатные скорлупы с применением материала лексан, который, как утверждают многие специалисты, обладает лучшими характеристиками ударопрочности и теплоустойчивости, чем распространенный АБС-пластик. Он поставляется в виде мелких гранул, упакованных в большие контейнеры. Затем поступает на станки формовки скорлупы, где плавится и заливается в форму для создания скорлупы, которая проектируется и изготовляется с помощью САПР/АСУ ТП. Процесс формовки каждой скорлупы шлема длится около 60 секунд. Формовочный станок автоматически выдает внешнюю часть формы шлема, после чего оператор снимает готовую поликарбонатную оболочку. После удаления литника скорлупа готова к следующему этапу процесса изготовления– пескоструйной обработке и покраске или подготовке под нанесение рисунка.
Надо отметить, что на заводе практически отсутствует запах и пыль, а рабочим не нужно надевать респираторы и иную защитную экипировку, поскольку условия работы чрезвычайно чистые.
На фотографии изображен один из станков для формовки скорлупы.
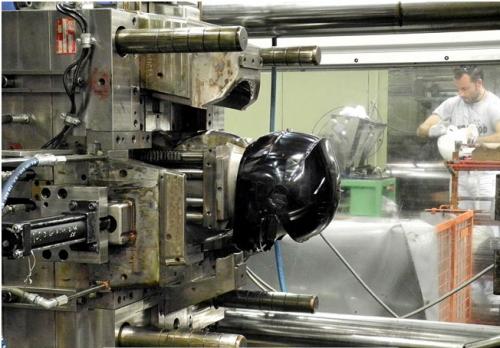
Каждый станок для формовки весит до 4 тонн

Скорлупа, только что снятая с формы и готовая к пескоструйной обработке и подготовке под покраску
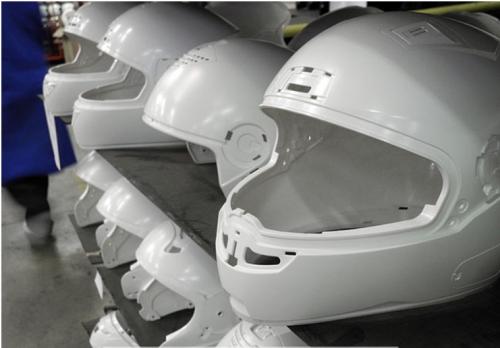
Гранулы лексана
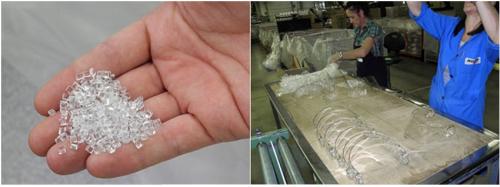
Этап III: Пескоструйная обработка, подготовка под покраску, нанесение переводного рисунка и покраска
Одним из преимуществ формованной поликарбонатной скорлупы является то, что все вентиляционные и обзорные отверстия для визора создаются в ходе формовочного процесса. Поэтому по окончанию процесса формовки скорлупа уже готова к покраске без дополнительного просверливания необходимых отверстий.
Процесс пескоструйной обработки скорлупы далеко не из приятных, поэтому для выполнения этого задания компания Nolan использует роботов. Перед покраской скорлупа шлифуется; это необходимо для того, чтобы поверхность стала гладкой и краска легла на нее ровным и плотным слоем.
После этой подготовительной работы скорлупа сразу поступает в камеру автоматической покраски. Переводные рисунки художники разрабатывают на компьютере и затем распечатывают на большом листе. Рисунок переносится точно так же, как и картинки, которые в детстве мы переводили на руки: он смачивается теплой водой и прижимается к предмету, затем отклеивается бумага.
После покраски и нанесения рисунков шлемы поступают в камеру автоматического нанесения прозрачного финишного слоя «Hi-Brite». Этот слой создает ощущение высочайшей прочности и защиты. Удивительно то, что для его изготовления используют формулу на водной основе, которая была разработана Nolan совместно с поставщиком краски.
После покраски и нанесения финишного слоя шлемы готовы к финишной сборке.
На фото ниже изображены готовые к шлифовке, покраске или нанесению рисунка шлемы. Все отверстия для вентиляции и других деталей уже готовы.
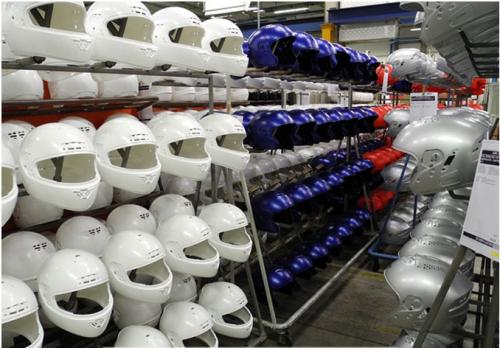
Робот производит пескоструйную обработку в закрытом помещении
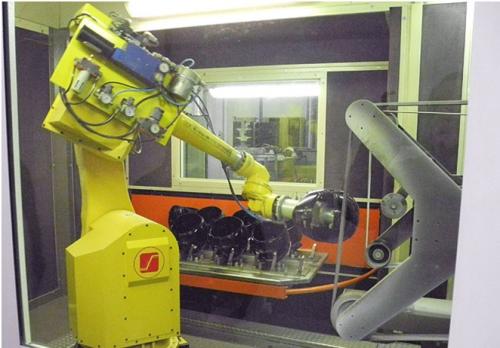
Цех нанесения рисунков. Внутри тепло и влажно, что необходимо для надежного нанесения рисунка на шлем:
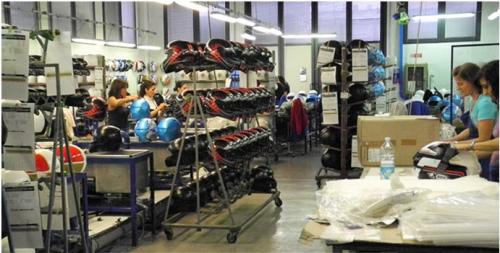
Нанесение рисунка на X-Lite X-802R
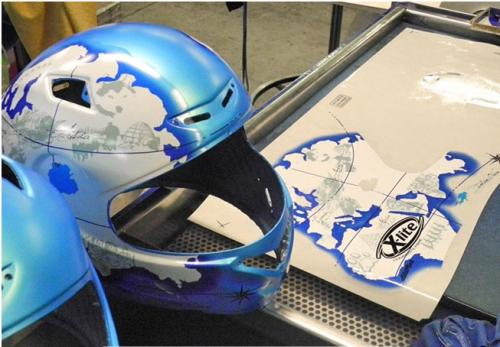
После нанесения рисунков, шлемы поступают в камеру автоматической покраски для нанесения финишного слоя «Hi-Brite»
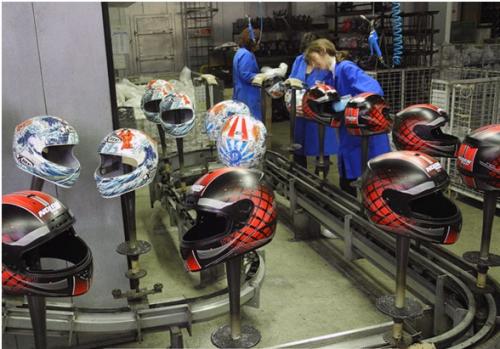
Этап IV: Заключительная сборка, упаковка и отправка
Итак, путешествие почти подходит к концу. После покраски и нанесения прозрачного слоя, шлемы отправляются к специалистам, которые устанавливают визоры и другие детали. На этапе заключительной сборки каждый шлем заново проверяется. Затем на него наклеивают защитные наклейки, после чего упаковывают вместе с инструкцией в коробку. Вот и все – шлем готов отправиться на полки магазинов, где будет ждать своего покупателя!
На фото ниже изображен цех заключительной сборки
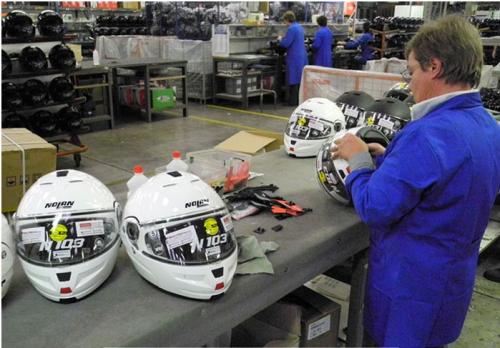
rita_eremina
- Рита
- 24 апреля 2013 в 17:50
- 2
- +39

- Bulavchatuy
- 24 апреля 2013 в 18:34
- ↓
Не такой уж Nolan и бюджетный. Приобрел на этот сезон N 103, единственный минус наверно шумноват, правда я на это внимания не обращаю, а в остальном просто супер.

Я юзал Xlite так как его мало кто тут может поюзать!
Головой об асфальт да и не один раз! Отработал на все 100! После последнего хайсайда он треснул!
Сейчас у меня топовый Шое и Xlite ничем не хуже!
Все давно знают что Арай это бренд который не стоит того бабла которое за него просят!
А вот ты наверное действительно не юзал Xlite ))
Головой об асфальт да и не один раз! Отработал на все 100! После последнего хайсайда он треснул!
Сейчас у меня топовый Шое и Xlite ничем не хуже!
Все давно знают что Арай это бренд который не стоит того бабла которое за него просят!
А вот ты наверное действительно не юзал Xlite ))

У меня есть и Arai RX-7 и Nolan X-lite-802.
В аре нет пинлока в наборе, в неолане есть +
В аре из за боковых «Ушей» на визоре остаются задиры (видно при открытии)
Покрытие на Аровских визорах (ну к примеру модный бензиновый) задирается от протирки его солфеткой. Многие от части переходят на шои по этой причине.
Снятие визора на Аре, отностительный танец с бубном, то есть на видосах все легко, а на деле не фига. Приятель так ушатал одно ухо на шлеме. Отломился крепеж уха (частично)
У X-802 человечие крепелние визора. Снимается без бубна (кнопку нажал и все) нет мелких деталек (как к примеру у AGV)
Оба шлема достойные. Но Арай сильней раскручен. Вот по этому цена в панавто 38 т.р. за RX7-GP, а за неолан X-802 26 т.р.
Как то так.
В аре нет пинлока в наборе, в неолане есть +
В аре из за боковых «Ушей» на визоре остаются задиры (видно при открытии)
Покрытие на Аровских визорах (ну к примеру модный бензиновый) задирается от протирки его солфеткой. Многие от части переходят на шои по этой причине.
Снятие визора на Аре, отностительный танец с бубном, то есть на видосах все легко, а на деле не фига. Приятель так ушатал одно ухо на шлеме. Отломился крепеж уха (частично)
У X-802 человечие крепелние визора. Снимается без бубна (кнопку нажал и все) нет мелких деталек (как к примеру у AGV)
Оба шлема достойные. Но Арай сильней раскручен. Вот по этому цена в панавто 38 т.р. за RX7-GP, а за неолан X-802 26 т.р.
Как то так.

Это точно, Хлайт и вся его система, визорная механика, пинлок, вытаскивание прокладки доставляет удовольствие пользоваться и очень хорошо продуманно.
Единственное как минус мозжно сказать, что он шумноват на скорости за 200 км/ч, ну дак извините х802 это рэйсинг шлем. Зато аэродинамика рулит и бошка даже на 300 км/ч не болтается туда сюда от ветра.
Хочешь комфорта и меньше шума бери туринг шлем.
Единственное как минус мозжно сказать, что он шумноват на скорости за 200 км/ч, ну дак извините х802 это рэйсинг шлем. Зато аэродинамика рулит и бошка даже на 300 км/ч не болтается туда сюда от ветра.
Хочешь комфорта и меньше шума бери туринг шлем.

- rita_eremina
- 26 апреля 2013 в 13:43
- ↑
- ↓
Нет, насколько мне известно, самостоятельно ездили на фабрику и изучали процесс. Это же, к сожалению, всего лишь переводная статья с www.webbikeworld.com
Только зарегистрированные пользователи могут оставлять комментарии.
Войдите, пожалуйста, или зарегистрируйтесь.
Комментарии (20)
RSS свернуть / развернуть